Consistent concerns we hear from customers always tie back to cost savings, efficiency, and reliability. The ROTO-JET® RO-FT between-bearing design pump is designed to help drive savings and improve reliability and efficiency for low-flow, high head service in the petrochemical industry.
We’re excited to share a few case studies below where our technologically advanced RO-FT pump has been used to just that.
A major US-based refiner was experiencing very high maintenance costs with a high-speed, integrally geared pump. Over three years, 17 seal failures occurred, resulting in major US OSHA LDAR VOC emission violations and approximately $100,000 in maintenance costs.
Because of consistent upsets, the process—a propane iso-butane mix—necessitated a pump that could operate over a wide range of flow rates (40-120 GPM. / 10-30 m3/h) without incurring damage to the pump or seals. However, the customer’s’ current OH6 pump could not handle the process upsets and was consistently experiencing multiple seal failures per year.
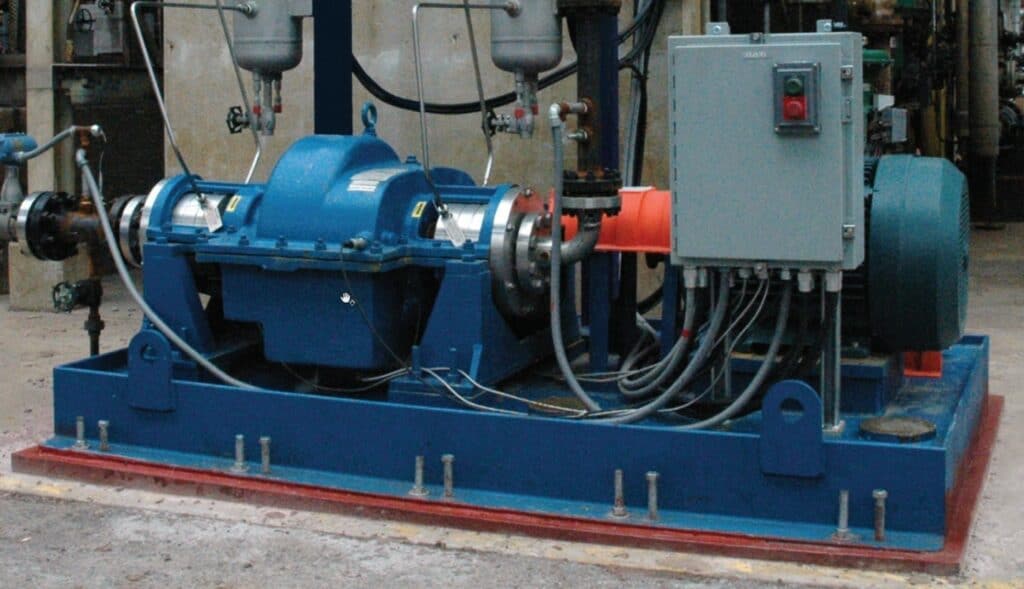
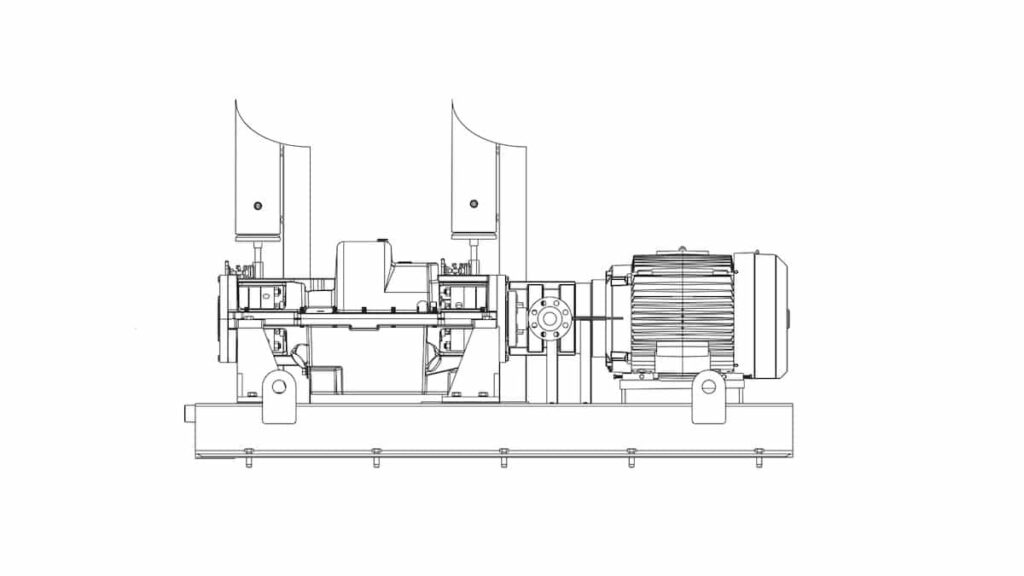
Based on prior successful experience with a Roto-Jet pump operating in upset process conditions without any damage to the pump or seals, the Reliability Engineer selected the fully API 610 compliant Roto-Jet RO-FT between-bearing pump to resolve the pump issue and improve overall plant reliability.
A testament for reliability comes from a major refiner, who has one the highest industry standards for Mean Time Between Repair (MTBR). This customer wanted the most reliable pump possible for a new low-flow high-head process. Statistically, centrifugal pumps have higher reliability than positive displacement pumps, so their focus was to evaluate and select a pump that would have the highest chance of achieving their MTBR goals. In this application, pump seals are the “weak” link in hurting pump reliability.
Due to the RO-FT’s ability to operate over a wide flow-range without imparting any hydraulic radial load to the shaft, there is no shaft deflection at the seal faces, assuring the seals can achieve their maximum life. Similarly, the RO-FT does not experience any conventional recirculation that would also result in reduced pump life.
After considerable research and evaluation, the refiner purchased the Roto-Jet RO-FT between bearing pump because of its ability to outperform competitive pumps in this challenging application.
Another Trillium Flow Technologies customer based in South-Texas, USA, was generating excess propane from their process and was paying approximately $10,000 per day to have it trucked out of the facility. To eliminate the costs associated with trucking, the customer wanted to explore the idea of using a pump to increase the pressure to the point that the propane could be injected into an existing pipeline. The challenge was that the operating conditions were deemed extremely low-flow (15 – 55 GPM. / 4-13 m3/h) and very high head-rise (4,800 ft. / 1463 m.) and sourcing a pump which would be stable, efficient, and reliable under those operating conditions could be extremely difficult.
After careful review of the possible centrifugal pump options, the user selected the Roto-Jet RO-FT pump due to its ability to operate at a very low flow rate and a wide operating range without damage from hydraulic radial forces. The Roto-Jet RO-FT pump was installed, and our customer began to immediately realize the anticipated savings from using one of the best, most versatile, and reliable pumps in the industry.
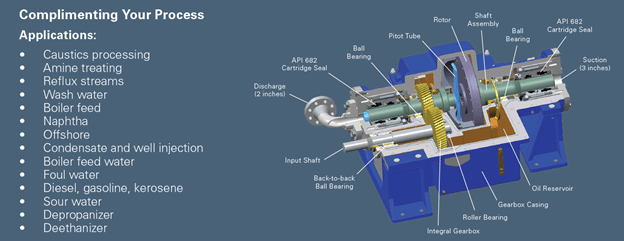
This article is published by
Trillium Flow Technologies™ serves customers in the power, oil & gas, general industry and water & wastewater sectors with highly engineered valves, pumps and actuators, as well as complete support in every phase of a project or …
Source of Article