Septage brought in by haulers used to be dumped into a six-inch pipe that went directly into the city’s main influent line, perhaps inevitably, (around once per month) backing up the old bar screen and washer compactor, creating an overspill. Meanwhile, due to abrasive grit, leaks – sometimes in the form of small waterfalls, would occur in pipes above the Facility’s old garage/service building, showering unsuspecting staff with the less than pleasant contents of wastewater.
Now, thankfully, the dedicated team of operators have much better starts to their day as a result of a three and half year, two-phase upgrade.
Like all treatment facilities, challenges are just part of a working day, but new grit-removal equipment and Septage Acceptance Plant have removed those very unwelcome episodes at this busy plant.
The after-effects of high-strength, sometimes shock-loading was certainly an ongoing issue, as it battled to strike a balance between taking in septage as a more than useful income, against the downside of the time/cost and labor to treat it. There was also the negative effect it would have on downstream equipment; not to mention straying into the territory of potential violations. At the WRRF built in the 1950s, with a grit chamber that was introduced during an upgrade in the early 1980s, the time had arrived to put some better infrastructure in place.
Dan Widdel, Vice President of Lakeside Equipment Corporation (Bartlett, IL), commented:
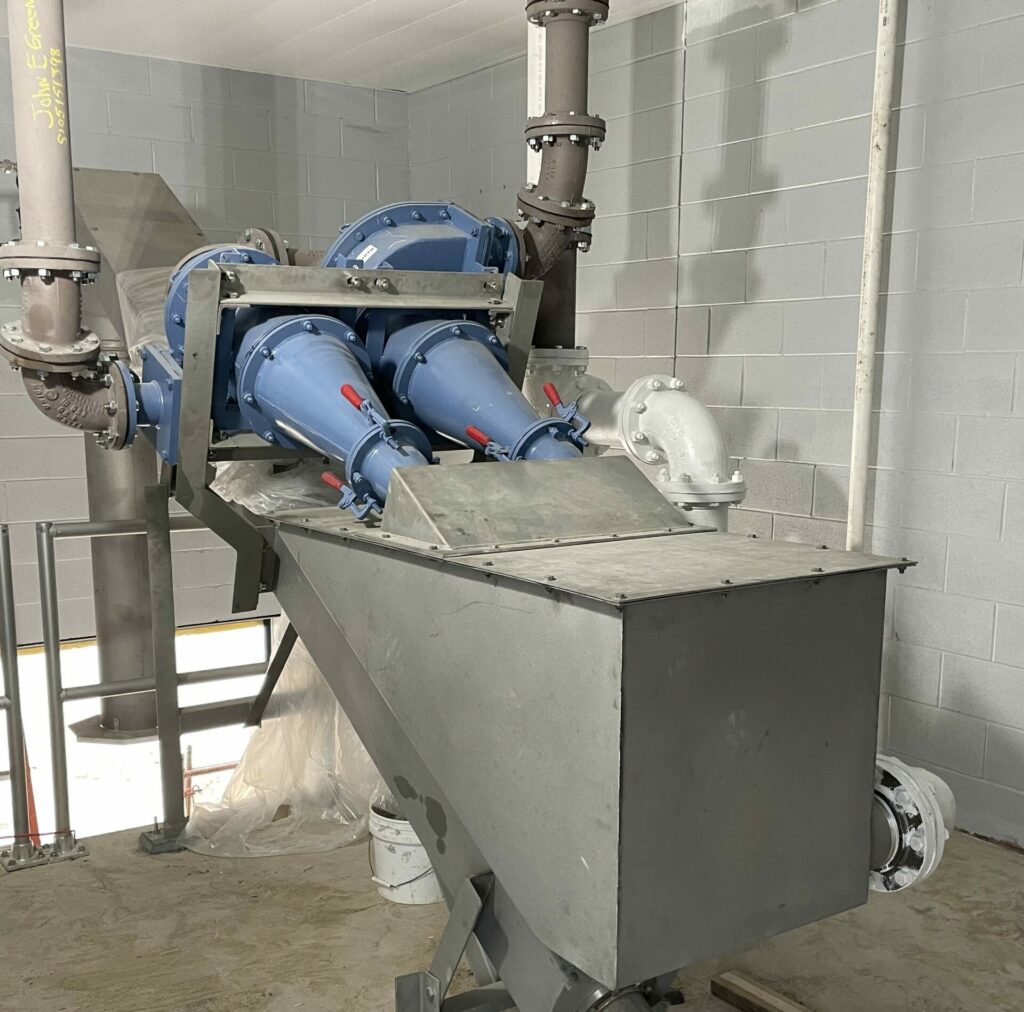
“We work closely with operators who work extremely hard to look after their facility, but sometimes, despite best endeavors, it can become a losing battle. In this particular case, the age of the equipment and the increasing flows with septage meant that maintenance has become very intensive.”
The City issued an RFP (Request For Proposal) for project design, which was awarded to a local engineering and environmental sciences business. Their design included two new grit channels, new vortex style grit removal equipment and a new septage acceptance plant. Lakeside Equipment Corporation was awarded the contract for this equipment through public bid from DuBois-Cooper Associates, which then brought together contractors and staff at the facility to fabricate and install Lakeside’s Spiragrit Vortex Grit Removal System and Lakeside’s Raptor Septage Acceptance Plant (SAP).
“Despite the tough applications,” continued Dan Widdel, “our customers expect at least 20-years-plus service from our equipment, and with it, a big reduction in maintenance hours. The operators at this facility were confident with the recommendation that DuBois Cooper made, based on many successful Lakeside installations across North America.”
‘Incoming septage is up by an average of 17% each year’
Even with all the monitoring that is carried out to look at the incoming nutrient levels, there are always some unknowns with septage. Previously, the facility didn’t have a comprehensive metering system, and having load-amounts written on tickets that then had to be handled, was very time-consuming. That’s all changed now, with a card that is assigned to each company, which is swiped at the facility, followed by entering a PIN to gain access. When the haulers are hooked up, they simply hit start and stop buttons to carry out their unloading. The new station provides administration capabilities to track and invoice customers, so the facility has freed up huge amounts of time. At the moment, haulers can gain access seven days a week, from 7.30am to 4pm, but the plan, eventually, is to make that 24/7.
‘The facility has reduced its maintenance costs by around 35%’
There’s been a small learning curve, going from manual to computerized operation, but the programming isn’t complicated, and the benefits are huge. Incoming septage is up by an average of 17% each year, and at the same time, the facility has reduced its maintenance costs by around 35%. The Lakeside septage and grit systems also help protect equipment further downstream in the process.
Removing debris and inorganic solids from septage tanks, grease traps, sludge, leachate and industrial waste, the heart of the Lakeside Septage Acceptance Plant (SAP) is its Raptor Fine Screen, which compacts and dewaters the captured screenings to a solids content of 40 percent. The screen’s rotating rake teeth fully penetrate the cylindrical screen bars, which prevents plugging and blinding from grease and small debris. This allows for faster unloading times to generate more revenue.
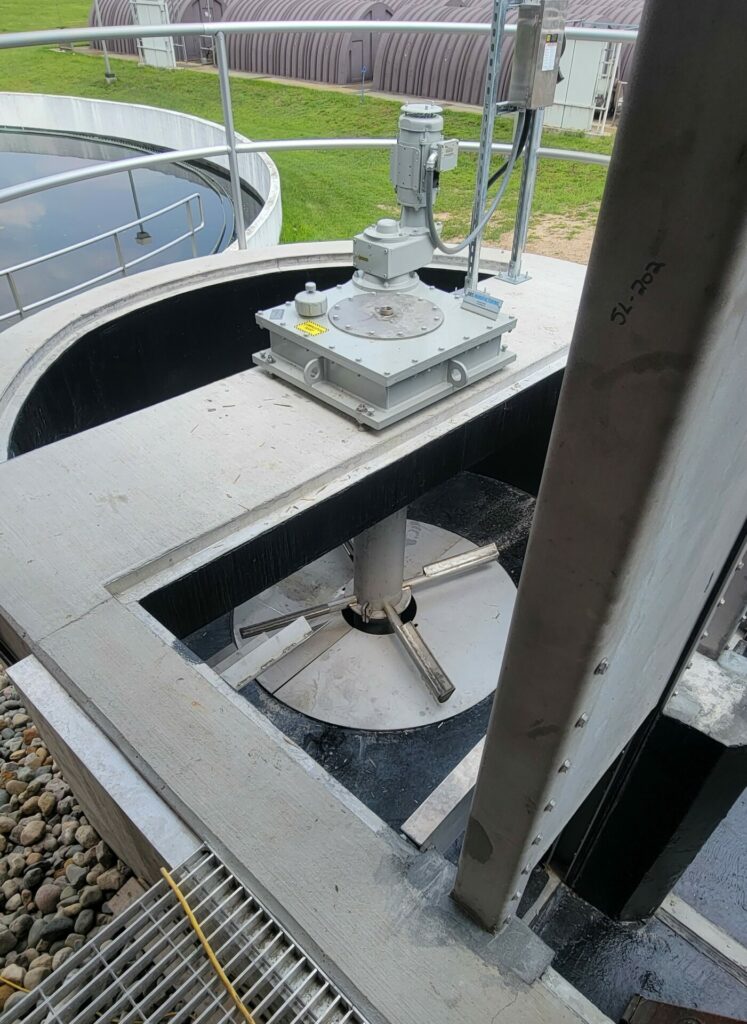
A new building to house the screening removal process has been very welcome indeed. Operators are no longer out in the elements, having to handle rags, grease, and messes. They are aware of what’s going on before entering the building, so, if ever required to shut the system down, can do so before entering or exposing themselves to hazards.
In this very abrasive application, having two units means that the facility now has redundancy, so one can be offline without forsaking continuous flow. To prolong the life of the equipment, operation at times can also be alternated.
Over a wide range of daily flow rates, the two Lakeside SpiraGrits remove inorganic grit from the WRRF in a mechanically-induced vortex environment. Rotating paddles maintain the flow velocity in the vortex chamber, keeping organics in suspension while allowing heavier grit to settle on the chamber floor. The settled grit then moves across the floor and falls into a lower grit hopper. A suction-lift grit pump sends the captured grit from the lower hopper to the Lakeside’s Grit Classifier for separation and dewatering. The classifier’s screw conveyor transports the settled grit for disposal, while the overflow is sent back to the grit chamber.
“Before this new upgrade,” added Lakeside’s Dan Widdel, “the facility had a square tank on the side of an old garage/service building, with a pump inside to send material up to a single classifier to remove grit and dewater. When equipment failed or became plugged, it sometimes meant operators having to run through streams of sewage to shut down the system! But now they have two separate tanks, all in one, so to speak. The mechanical equipment is no longer housed on the second floor, and like the septage system, can be shut off before encountering any unpleasant surprises.”
The vortex created by the Lakeside SpiraGrit(s) use centrifugal force to separate the grit, so another benefit is that it has removed the need for energy-hungry blowers. From a design flow of about four million gallons, each new tank is designed for seven million gallons, so the facility’s capacity has increased more than three-fold.
‘Fast-growing number of companies that produce marijuana’
In addition to septage, and of course the domestic wastewater from the City, the WRRF also receives effluent from a local tannery, and a brewery; the latter of which is typically high in nutrients. Most recently though, the Facility’s Industrial Pretreatment Program (IPP) has been getting to grips with a new phenomenon in the State; the fast-growing number of companies that produce marijuana, one of which has opened up right next door to the WRRF. $3 Billion worth of both recreational and medical marijuana was sold in the state in 2023; second only to California as the biggest cannabis market in the U.S.
As part of its IPP, operators go out to visit these new facilities. Loading is not expected to make a significant impact, but investigations will continue, because the number of processors keeps increasing.
The upgrade has also included a new holding tank, so instead of having to try and deal with shock-loads caused by the daily eight-hour septage deliveries, everything can be fed-in gradually.
“The biological process is so much better,” added Dan Widdel. “The facility still has to fight hard with ammonia and phosphorus throughout the year. Nutrient loading eases in rain events, but then can be a real challenge in summer. And in winter too, due to settling. The operators, like so many who are unsung heroes, should take huge credit for being such dedicated stewards of the environment, which they do everything they can to protect. People in the City and beyond take great pleasure in being close to or out on the local river; fishing, kayaking, tubing, and enjoying the wildlife, so the new screening equipment and all the hard work at the facility has a very positive impact.”
Source of Article