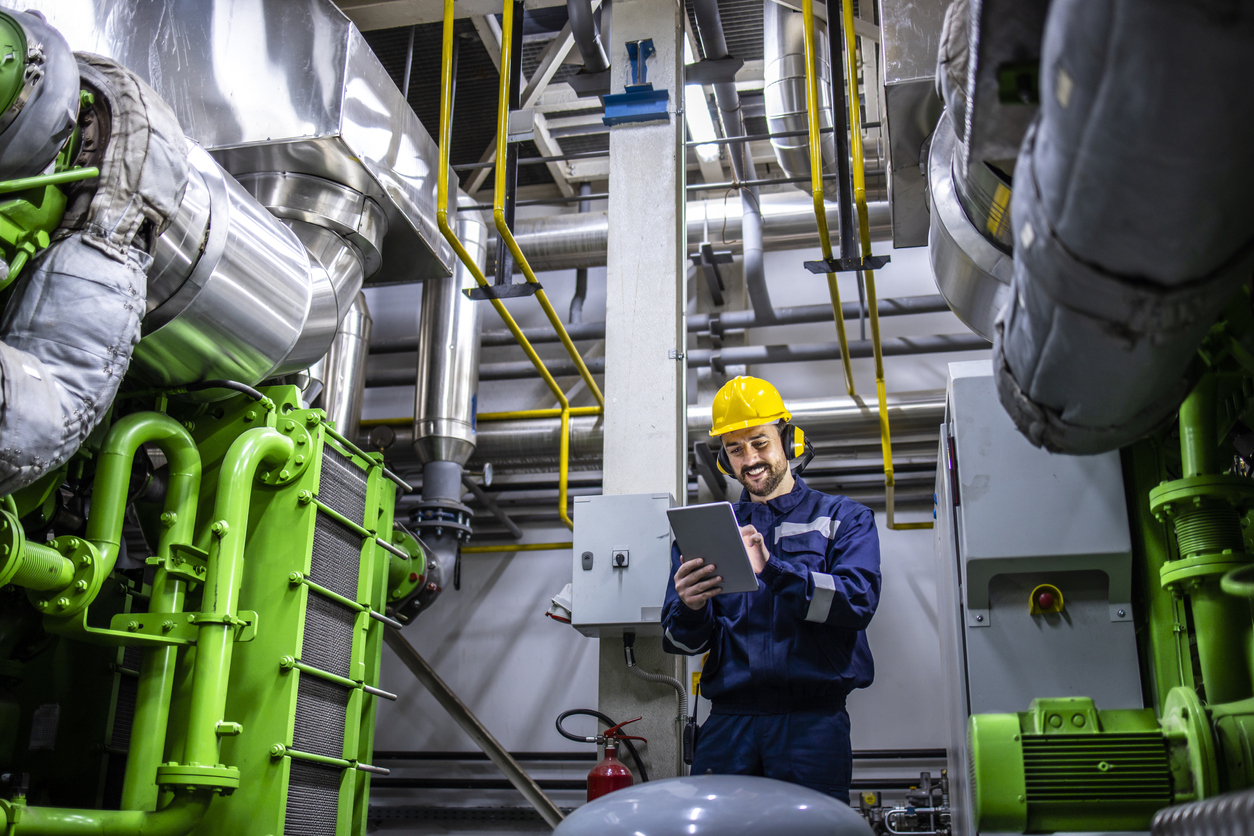
Understanding Predictive Maintenance: Predictive maintenance involves using data, sensors, and predictive analytics to foresee potential equipment failures before they occur. This proactive approach enables timely interventions, reducing the likelihood of costly breakdowns and unplanned downtime. In fluid handling systems, predictive maintenance aims to monitor, analyze, and predict the condition of pumps, valves, pipelines, and related components to optimize performance.
Critical Components of Predictive Maintenance
Sensor Technology: Sensors play a crucial role in predictive maintenance by collecting real-time data on parameters such as temperature, pressure, flow rates, and vibration levels within fluid handling systems.
These sensors provide continuous insights into the health and performance of equipment, enabling early detection of anomalies or deviations from normal operating conditions.
Data Analytics and Machine Learning: The collected sensor data is analyzed using advanced algorithms and machine learning techniques. Patterns, trends, and potential failure indicators are identified through data analysis, enabling predictive models to forecast equipment health and anticipate maintenance needs accurately.
Condition Monitoring: Continuous monitoring of pumps, valves, and pipelines allows for identifying early warning signs of potential issues. By tracking changes in performance metrics and comparing them against established benchmarks, maintenance teams can schedule interventions precisely when required, optimizing maintenance efforts and reducing costs.
Predictive Models and Maintenance Scheduling: Predictive maintenance models utilize historical data, current equipment conditions, and predictive analytics to forecast the remaining useful life of components. These models assist in developing optimized maintenance schedules, ensuring that maintenance activities are performed precisely when needed, minimizing downtime, and maximizing equipment availability.
Benefits of Predictive Maintenance
Increased Equipment Reliability: By detecting potential failures in advance, predictive maintenance minimizes unexpected breakdowns, improving the reliability of fluid handling systems. This leads to enhanced operational continuity and productivity.
Cost Savings: Predictive maintenance helps reduce operational costs by preventing costly unplanned downtime, optimizing maintenance schedules, and reducing the need for emergency repairs or component replacements.
Enhanced Safety: Proactively addressing equipment issues ensures a safer working environment by mitigating the risk of accidents or incidents resulting from equipment failures within fluid handling systems.
Extended Equipment Lifespan: Regular monitoring, timely interventions, and optimized maintenance prolong the lifespan of pumps, valves, and other components, maximizing the return on investment for these assets.
Conclusion
In the realm of fluid handling systems, predictive maintenance stands as a pivotal strategy to ensure operational efficiency, reliability, and cost-effectiveness. Industries can proactively manage maintenance, minimize disruptions, and optimize the performance of pumps, valves, pipelines, and related equipment by leveraging sensor technology, data analytics, and predictive models. Embracing predictive maintenance in fluid handling improves system reliability and contributes significantly to increased safety, reduced costs, and prolonged equipment lifespan.
Source of Article