Green energy projects are gaining momentum. Some pilot schemes are being trialed in order to provide proof of concepts but is this enough and can the planet really wait for the standard committee’s to decide which way to turn?
The task of decarburizing the complete energy chain is a herculean challenge. Processes that have been refined for several decades can not simply switch to a green equivalent overnight without considerable risk.
One piece of this complex challenge is the development of reliable, cost effective valves because according to the EPA over 60 percent of fugitive emissions come from gas valves. But how do you develop a safe and reliable product in such an emerging market when the standards that govern such products are yet to be written?
British company Oliver Valves have developed a solution with their advanced metal seated pipeline valve range.
Ball valves offer simple quarter turn operation together with an unrestricted flow path. Non-rising stems and compact geometries combine to make them the product of choice for many operators in a wide range of processes.
The metal sealing variant of the ball valve offers enhanced resistance to abrasives, extended reliability and prolonged service life in comparison to the more commonly used soft seat or polymer sealing alternatives. The design of metal seated ball valves also lends themselves to application with temperatures above 200 °C.
But creating a metal to metal, gas tight seal is no easy task. It required a complete and full understanding of the topography of the components, the stresses and the relative displacements in order to maintain the necessary contact stress to achieve a gas tight seal.
Fortunately the engineers at Olivers have gained over thirty years of metal-to-metal sealing experience through their sub-sea gate valves, all of which offer this level of performance.
In pipeline ball valves however, special consideration has to be given to the size and geometry of the ball and seat, both of which are complex in shape and their often asymmetrical nature makes the prediction of deflection at pressure difficult to determine.
Unlike a soft, more compliant seat, a metal seat has to deflect at the exact rate at which the ball deflects when subjected to full working pressure in order to maintain sufficient contact stress to create a seal. These deflections, although microscopic in nature can attribute to a leak in service if not managed correctly.
One solution would be to greatly increase the size and rigidity of the ball and seat in order to minimise any deflection, however the associated costs of the product assembly would increase exponentially. An increase in ball diameter would require a larger cavity size which in turn would increase the pressure boundary between the body and end. This increases the sealing diameter of the end connector which in-turn increases the blow out force of the end connector, resulting in need for larger fasteners or a greater quantity. Such fasteners need to be accessible using conventional tightening equipment which can also add to the overall size and of course cost of the finished product. So to avoid a cascade of increasing sizes and associated costs it is essential that the optimum size of ball is determined if the most cost effective, reliable solution is desired.
Using advanced FEA techniques the optimum size of the ball and geometry of the seat had been derived taking into account the strengths of materials suitable for hydrogen applications. These optimum sizes have then been tested at in-service conditions to validate the products performance at all temperature and pressure combinations.
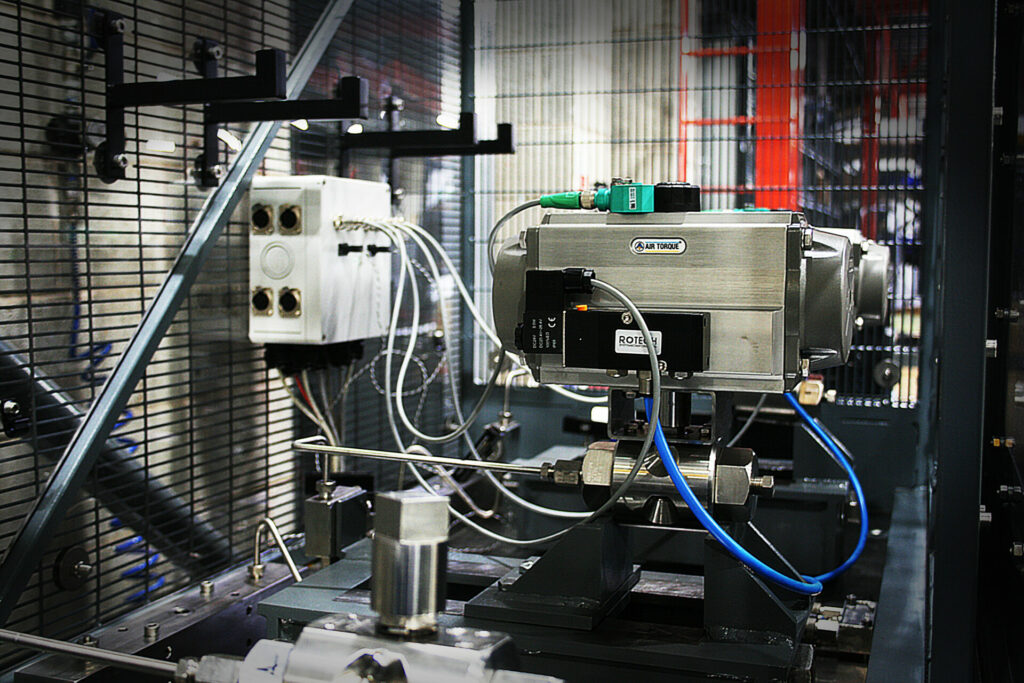
Michael Oliver, founder and chairman of Oliver Valves is passionate about invocation, investing in the future and can often be found problem solving and brainstorming with his engineers at the Oliver R&D facility in Cheshire. A factory dedicated to the development of their products and it is here that the engineers have derived their own hydrogen test standard. It incorporates the requirements of industry known fugitive emissions tests and enables simulation of in-service conditions including prolonged operations. The qualification focuses on the attributes associated with pipeline valve applications and requires operational and seat leakage tests to be performed at maximum and minimum rated temperatures whilst monitoring for fugitive emissions. However to show case the performance of their zero leakage metal sealing range the qualification was extended to include 3000 operations after which the valve still remained bubble tight at both working pressure and within acceptable fugitive emissions rates.
Nick Howard, Director of Market Development at Olivers says, “ By harnessing the years of metal sealing experience and combining it with our in depth knowledge of hydrogen applications, we have been able to develop metal-to-metal sealing ball valves that have the reliability and prolonged service life of a metal seated valve but with the sealing performance of a soft sealing valve. This is a real mile stone for the industry.”
Granted, valves are a small piece of a large and complex problem but should further initiatives be offered to companies to accelerate the development of their products? After all is it ideas we are short of or ways to convert our ideas into reality?
Source of Article