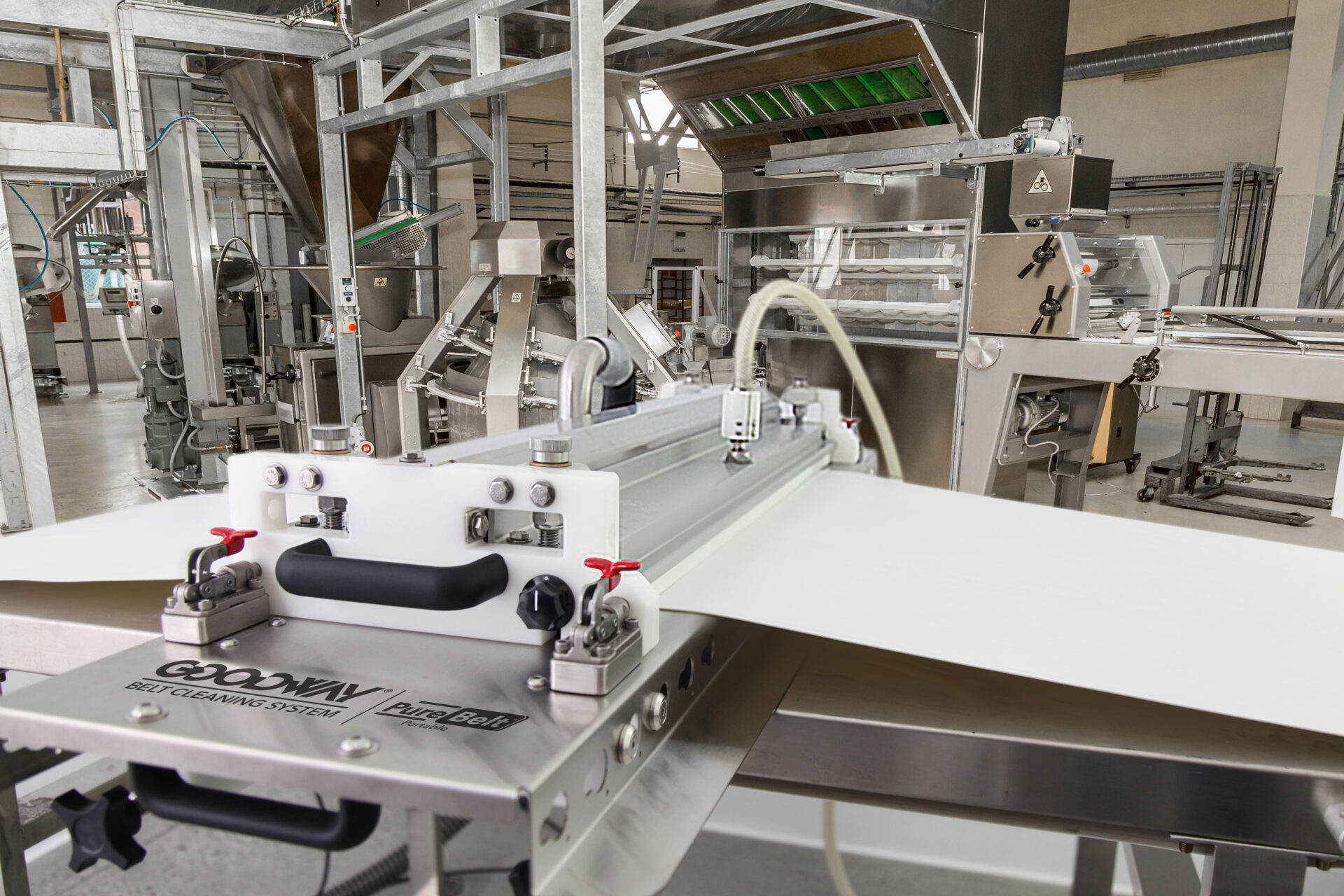
Frequency of Cleaning
The frequency needed for cleaning a food processing conveyor belt depends on several factors. One of the considerations is the amount of soil that accumulates on the belt. If the belt soil builds up quickly, more frequent cleaning is necessary to minimize the risk of contamination to other items. Another critical consideration is the type of food transported on the conveyor belt. Sticky foods, for example, tend to accumulate more quickly than dry goods, making them more prone to contamination and requiring more frequent cleaning.
Methods of Conveyor Belt Cleaning
There are three approaches typically used to clean a conveyor belt system; manual cleaning, semi-automated cleaning, and fully automated cleaning.
Manual cleaning is very time consuming. Facilities using this method allocate labor resources and experience production downtime for often inconsistent results. With a semi-automated cleaning method, facilities see quicker results by combining manual cleaning with some automated systems – dry vacuuming loose contaminants, spraying and rinsing, etc. This method will be less time consuming but still will need allocation of labor and can require a significant level of expertise. With automated cleaning, the return for the up-front investment is realized quickly with minimal labor needed and greatly reduced production downtime while delivering a consistent cleaning.
Goodway has been on the forefront of innovation for cleaning and sanitation of conveyor belt systems, combining the power of dry steam with the efficiencies of automation.
“Food safety is top of mind for food production and processing facilities and Goodway Technologies is committed to finding automated and effective solutions that help reduce labor costs and keep production lines running,” said Tim Kane, President and CEO of Goodway Technologies. “Performing cleaning and maintenance isn’t optional, but our solutions can make it easier and more effective to create a safe and clean environment.”
Goodway recently launched PureBelt™, a line of automated, clean-in-place conveyor belt cleaning systems for flat and modular plastic, wire mesh, and bottling line belt cleaners. PureBelt systems are powered by low moisture, dry steam systems, which deliver powerful cleaning and sanitation performance by eliminating allergens, mold, yeast, bacteria, and other soils. Goodway Technologies manufactures three conveyor belt cleaning systems that can be customized to meet the exact conveyor dimensions.
This advanced technology uses 90% less water than traditional cleaning methods making it ideal for equipment where water needs to be minimized or avoided or where chemical cleaning is not preferred. Not only do these systems lower operational expenses with reduction in water usage but they help facilities save on labor costs and production downtime. See how this facility reduced cleaning time of their conveyor belt systems by 99% by implementing a PureBelt automated conveyor belt cleaning system.
Source of Article