According to Nicola Zenoni, Engineering Manager at IMI STI, increasing scrutiny on plant teams to optimise processes means the risk and impact of system failures and other costly disruptions has become even greater. He is, therefore, encouraging processing professionals to audit existing operations and ensure effective tools and solutions are in place to observe and analyse plant production.
“Being able to measure and monitor performance has always been vital to ensuring consistent plant operations, especially in facilities working with expensive operating machines – and particularly those involved in critical processes or safety-related processes,” he explains. “Consequently, being able to monitor component conditions more accurately should be expected as standard, especially considering the consequences of not doing so.
“For example, turbine trip events can lead to wide differential pressures inside the turbine bypass valve, resulting in vibration, noise, and erosion that can compromise plant performance. By contrast, accurate control of the flow inside the compressor, managed by the anti-surge valve, can help to support more efficient and safe operating conditions while helping reduce surge events.
“Given these risks, plant managers should consider the role of digital pneumatic positioners in guaranteeing ongoing valve care and integrate these solutions into existing operations where necessary. The online and offline diagnostic support provided by these solutions will be crucial in ensuring maintenance teams can adapt to a constantly shifting plant environment.”
With these issues in mind, IMI’s specialist actuation brand IMI STI has recently developed a high-capacity and high-precision digital pneumatic positioner. The Smart High-Performance (SHP) Positioner, which supersedes IMI STI’s existing FasTrak (FT) Positioner, uses a control algorithm system and patented logic to ensure very low stroking times with high dynamic control, mitigating issues from all applications.
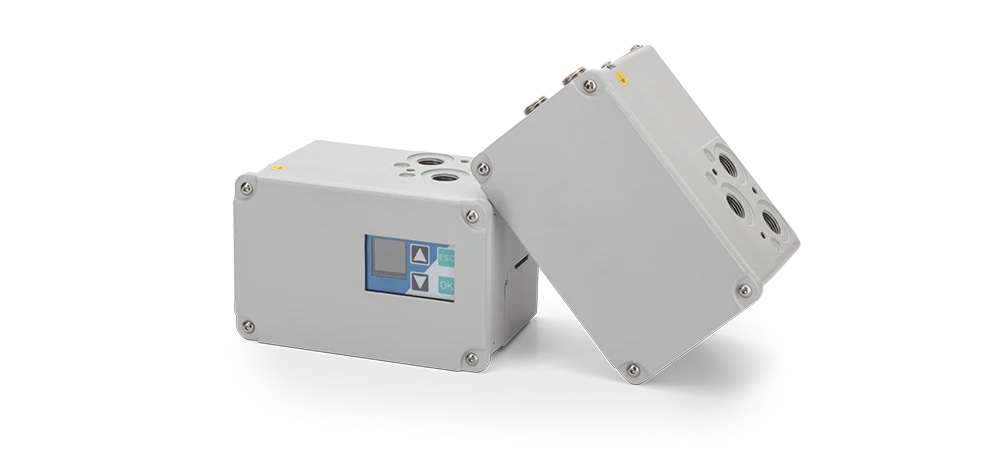
The solution’s unique design also provides dynamic, high-speed performance in large-volume actuators, minimising the need for accompanying flow amplification devices. It also features a vibration-resistant, contactless feedback sensor, providing high-quality, valuable information detailing valve performance. According to Mr. Zenoni, the diagnostic tools featured in solutions such as the SHP Positioner will be essential to allowing greater control over future plant operations and limiting potential downtime.
“In demanding applications and environments, the importance of gathering data during regular service operations through tools such as recorders, counters, and event logs cannot be overstated,” Zenoni concludes. “Using solutions that not only record this information, but interpret it to provide valve life predictions and updates on overall system status is invaluable for minimising maintenance activities, allowing predictive analysis, and ensuring safe process handling.
“Combined with the ability to offer offline diagnostic procedures including ramp, step, valve signature and frequency, and other available tests, digital pneumatic positioners are well-placed to help industrial plant stakeholders avoid unplanned plant downtime and production losses. Given the potential harm that undesired flow rates can inflict on critical components such as compressors, turbine bypass systems, and superheaters, it is imperative for processing professionals to proactively assess the positive influence solutions like the SHP Positioner could bring to their operations.”
Source of Article