The new generation of globe valves with fully body-guided disc have an excellent ability to handle flow at high-pressure differentials.
API 623 in its new edition requires that all globe valves must have their disc fully body guided, in order to hold the disc for supporting the hydraulic forces and vibrations when the valve is in severe throttling. The main purpose of this design is not to transfer lateral forces to the stem, because the allowances between the stem and the disc are larger than the allowances between the body guides and the disc. This keeps the valve packing in position and prevents leakage.
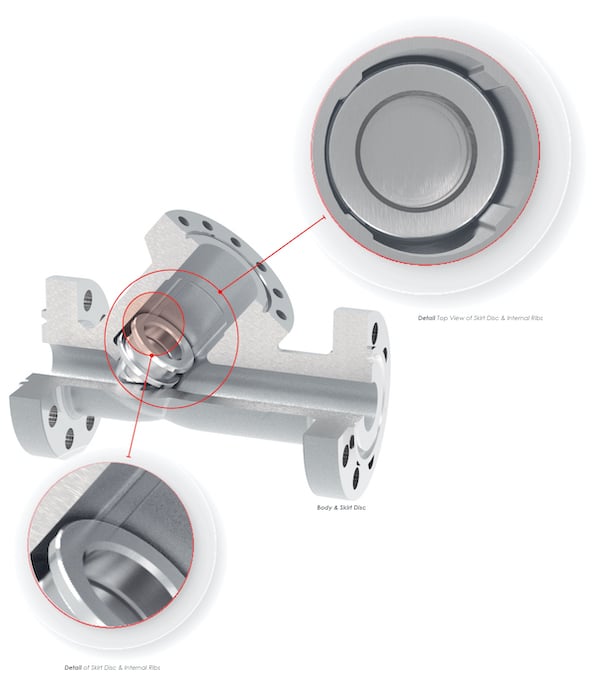
This is a requirement from the new API standard, but there are other considerations must be taken into account. The different surface materials in the seating area provide the capability of high flow regulation in the globe. In the following figure we show different materials subjected to severe throttling during 150 days and the results in material weight loss are shown below. While practically all materials show erosion, Stellite material has the capability to absorb impulsive force of the flow. When the high regulation of the flow is a requirement, the surfaces of the seat ring and the disc must be covered with Stellite.
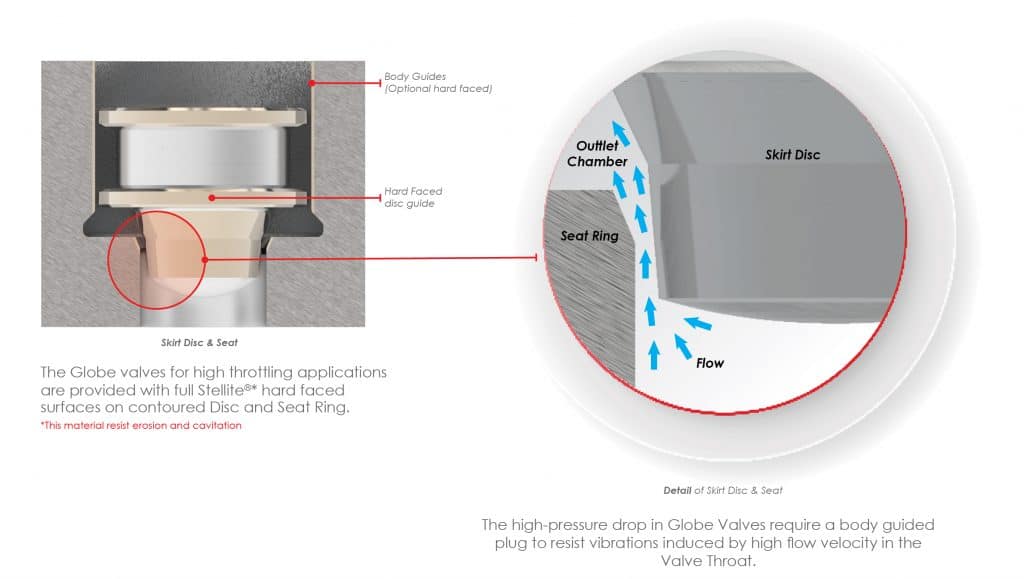
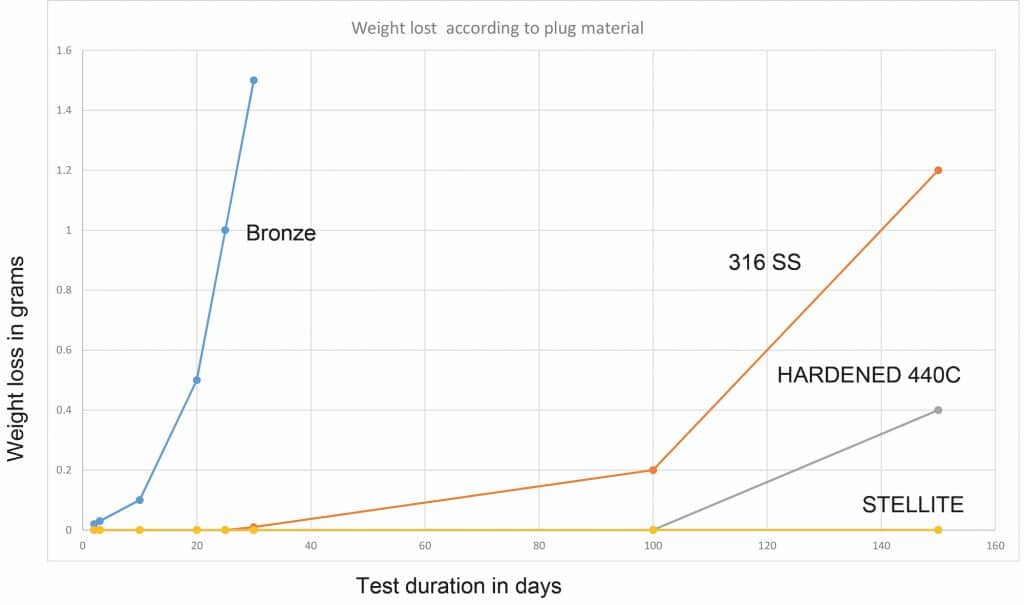
Other consideration in selecting Globe valves is what many people name “Turn down value”, that is to say the flow reduction capability of a globe valve that is a relationship of the maximum provided Cv in relation to the minimum Cv that the valve can handle. The “Turn down value” is expressed in values like 4:1, 8:1, and a maximum of 10:1. For “Turn down values” of 8:1 or higher the usage of a “Skirt Disc” is required.
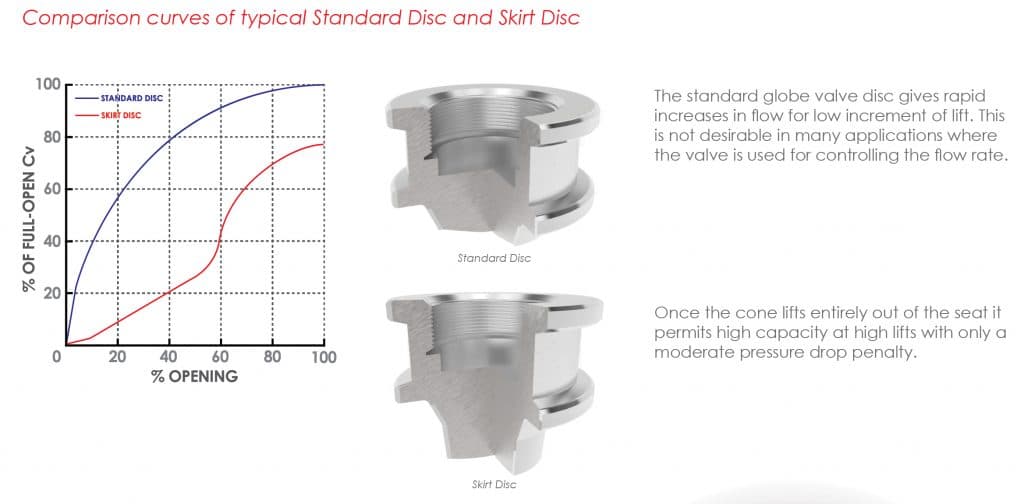
When selecting a Globe valve, the parameters of:
a) Type of fluid
b) Inlet pressure & Inlet temperature
c) Flowrate
d) Required pressure drop across the valve
Are necessary for determining the size of valve, the body configuration (like “Y” pattern or “T” pattern), normal size or a Venturi type, the type of disc (Standard or Skirt). All of this is required in order to assure that the selected valve has the capability of handling the required flow at a certain pressure drop. The Noise generated can also be predicted, and if incipient cavitation is present. The body configuration can change the flow capability as shown in the figure bellow:
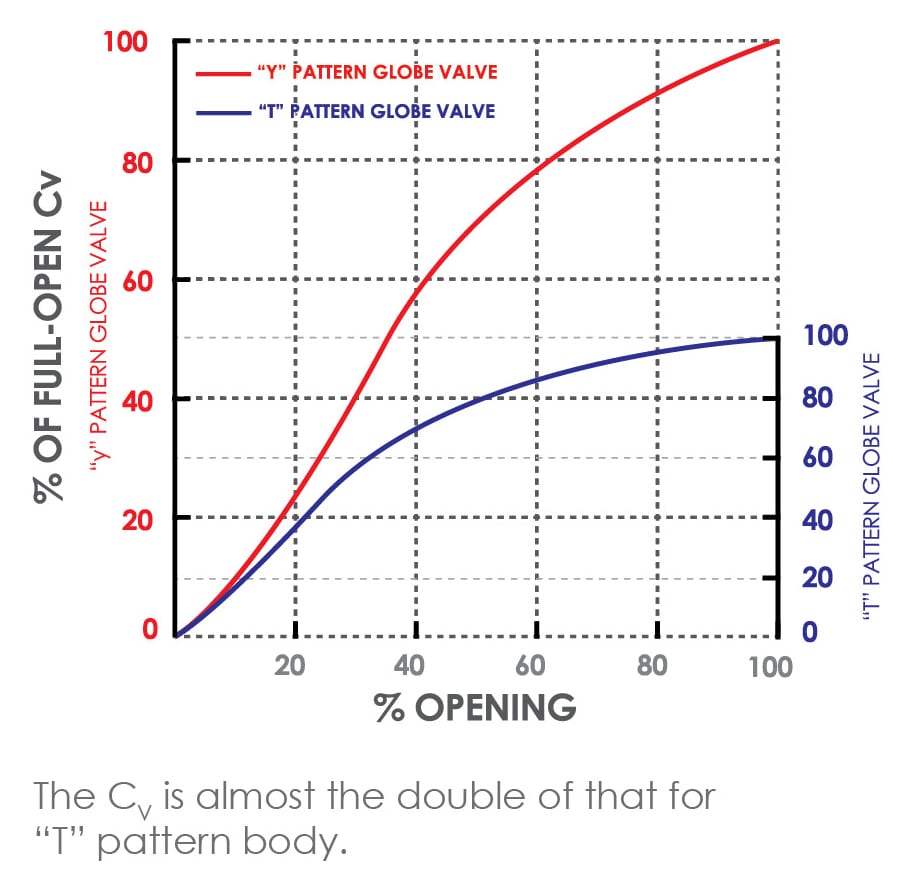
Although is not the intention of substituting a control valve which is specifically designed to control de fluids in a permanent performance. Frequently, manual Globe valves are used to do the job of a control valve during short periods of time while the steady control valve is took apart from the line for maintenance purpose. If the manual valves are not designed for that special throttling, they can be destroyed in that short period.
In other words, the globe valves should not be installed as if they were “commodity valves”, just for isolation. Many problems are present now in power plants or refineries due to the fact that the globe valves are considered “commodity valves”.
Other important aspect of the globe valves is the capability of transforming them in automated valves by using an electric or pneumatic actuator. The way to achieve this purpose is by manufacturing the globe valves with a non- rotating stem that moves only up and down. Most of the “commodity valves” come with a rotating raising stem that require sophisticated actuators to automate those valves. Also it has been demonstrated that non rotating stems protects the valve packing and provide better performance in low fugitive emissions.

It is our intention to make globe valves specially designed for severe service and to select the best globe valve configuration for the end user intended service.
About the Author
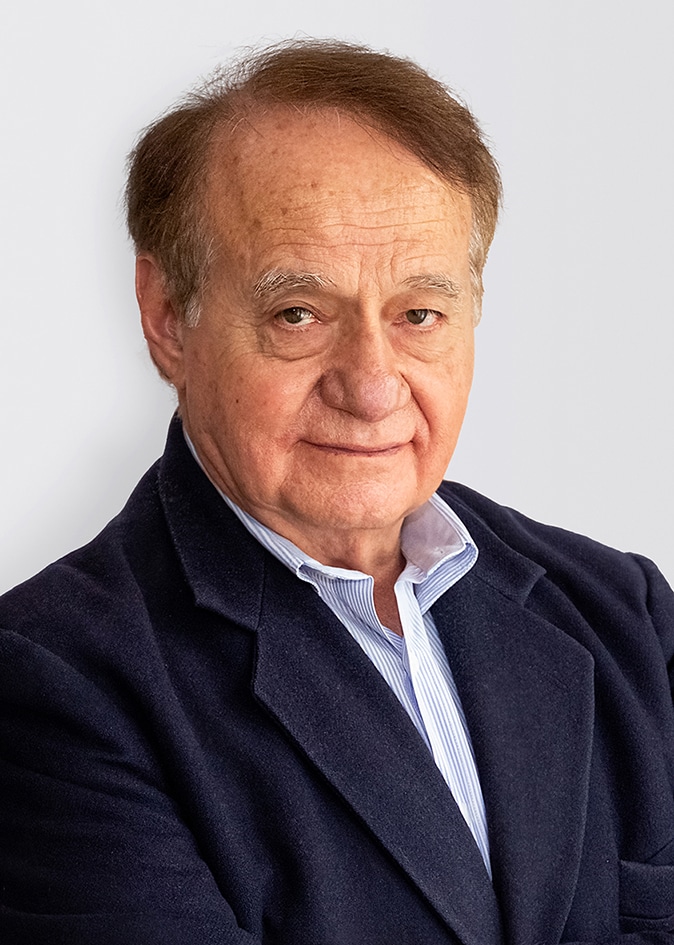
Felipe Ruiz de Chávez, Professional Engineer, Head of Engineering Department of Xanor de México has 44 years of experience in design and manufacturing of industrial valves.
With more than 15 years of participation in API standards and voting member of MSS (Manufacturers Standardization Society of the Valve and Fitting Industry). He also participates in Pemex and CFE standards.
Click here for more informationClick here for related articles and newsSearch for valve manufacturers in our equipment guide
Sign up for Process and Control Valves E-Updates
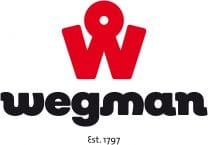
Founded in 1797 and providing customers with valve & actuator solutions from our representations Cameron (Orbit, General Valve, WKM, Grove, Ledeen. Entech, Douglas Chero, Demco, , Newco, Maxtorque, Dynatorque (Tom) Wheatley), Xanik, ISV, QTRCO & UNP Polyvalves. Many products can be supplied with short delivery time, besides the brands we represent …
Source of Article