Accidental spillage of oils and other chemicals from industrial sites causes a significant amount of pollution every year. Many spills can be prevented with rigorous production processes and strict monitoring. But if there is an accidental leakage, it’s important to act quickly to:
- Minimise possible damage: spills can spread rapidly and seriously harm the environment
- Avoid prosecution: court fines and clean-up costs after a spill can be expensive
- Reduce negative PR
What is spill control, primary and secondary containment?
Spill control tactics are designed to reduce the amount of contact the spilled material has with people, property and the wider environment.
Primary containment is the actual vessel or container holding a substance – solids, liquids, chemicals or waste. It’s the first line of defence against spills, leaks or accidental releases.
Secondary containment serves as a back-up in case the primary containment is breached.
It is a regulatory requirement for any primary container if the contents are hazardous, and a breach of that containment would endanger life, soil or water around it.
By law, the secondary containment system, ‘must have sufficient capacity to contain at least 10% of the total volume of the primary containers or 100% of the volume of the largest container, whichever is greater.’
Our specification for this client
For this particular project, our client asked for a pump which would be corrosion resistant not only to a number of differing fluids but also resist deterioration overtime from exposure to air, and water which can be common with pumps manufactured from Cast Iron. We specified the pump to be manufactured from AISI316 stainless steel to ensure that there were no issues with pump corrosion during its operation lifetime.
We specified a 3’ horizontal self-priming pump made from cast AISI 316 stainless steel. This material is widely used in industrial applications. It’s also well suited to even harsher environments needing greater corrosion resistance, having more tensile strength at higher operating temperatures.
Our stainless steel self-priming pump was specially designed for spill containment at the client’s site where there are several tanks and silos housed within a bund – this is a type of embankment or wall of stone or earth, built to stop the area being covered by a large amount of water.
Also suitable for tanker loading
In addition, the pump will be used as a tanker loading pump and to feed discharge into a sewage plant. If the silos or tanks ever leak, the pump will evacuate the bund of any wastewater, milk or other low viscosity liquid.
We supplied the pump with a built-in control panel so that users had convenient local control of the pump’s operations on site.
A key feature of this spill control and tanker loading pump is the self-priming function which primes the pump in just 45 seconds – vitally important when a spill has to be contained quickly. In addition, it can handle solids up to 30mm and dry run for up to 30 minutes once the head is filled with liquid.
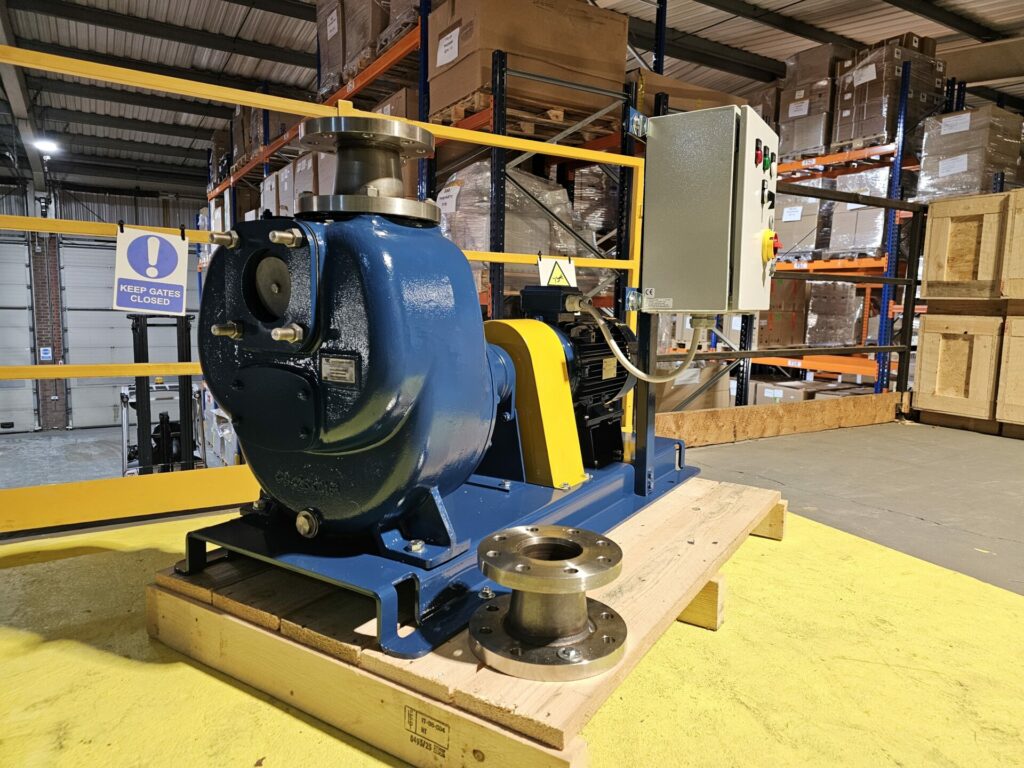
Source of Article