Within industrial positive displacement pumps, there are many options to choose from, such as gear, peristaltic hose, piston/plunger, progressive cavity, or air operated double diaphragm pumps. So, how to choose which one suits you the best? Luckily, one pump combines both reliability and versatility, in addition to other advantages: AODD pumps. Wide application range Versatility is the main advantage of air operated double diaphragm pumps, as they are capable of pumping a wide variety of fluids. These range from shear sensitive fluids to slurries or even abrasive/corrosive fluids and, by choosing the right design and the right materials, they are able to meet the installation requirements without causing damage to the pump or the final product. Another important aspect is that the fluid does not necessarily have to be clean, it may contain sus-pended solids, making them suitable for even the most severe applications and working conditions
Given their versatility, they can be found in many industries. They can be used for transferring acids in the chemical industry or for slip transfer in the ceramic industry. This demonstrates the pumps wide range of use and how they can adapt to any application. The most common uses are tank loading/unloading, fluid batching/mixing, recirculation and transfer, water extraction and treatment, coating and mold filling. Such uses can be found within the following industries:
- Petrochemical
- Mining and construction
- Paint and coatings
- Pulp and paper
- Textile
- Mechanical and plant engineering
- Ceramics
- Marine
- Power stations (energy)
- Tank farms/ bulk transfer
- Waste water and water treatment
- Electronics
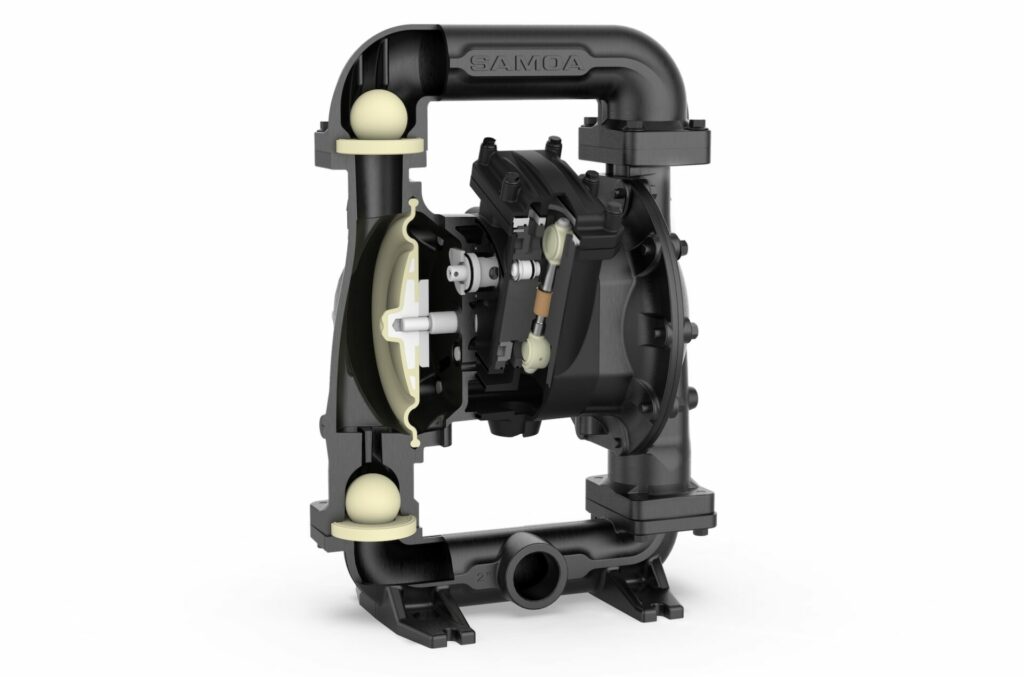
In addition to their versatility, these pumps provide a series of competitive advantages compared to other technologies, in terms of performance features and cost reduction. These pumps are capable of running dry without damaging the pump and they do not build up heat during operation. In addition, they are self-priming and ideal for suction lift applications. They are safer than other pumps, as they do not have any electrical hazards, they can be used in explosive atmospheres (ATEX certified models) and can operate completely submerged without diminishing their performance.
In addition to their performance, they are an economical choice for a wide range of applications when compared to other pump technologies due to their ease of operation and maintenance. These pumps start automatically when the fluid outlet is opened which makes it simple and easy to integrate into a pumping system. Also, the fluid discharge pressure and flow rate are easily adjustable by using only one air pressure regulator. The absence of mechanical and dynamic seals makes service faster and easier, thus reducing the cost and time required to restore the pump.
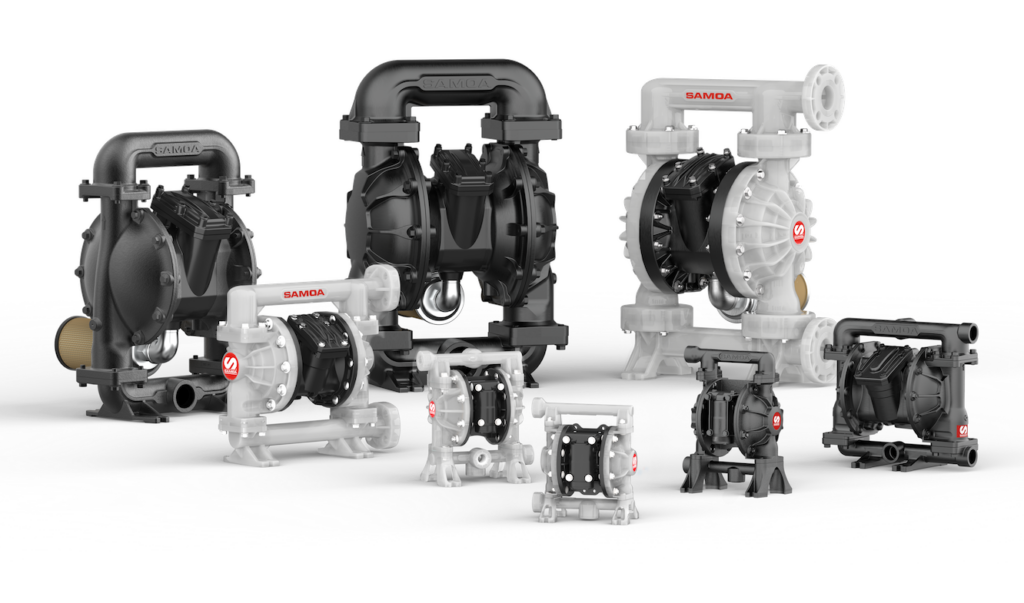
Common uses and pump sizes Diaphragm pump can be classified based on their size and industry of use. According to this we can consider the following categories:
Applications using inks or paints: 1/2″ metallic pumps are often used for pumping ink or paint, as long as the fluid has low viscosity (less than 10,000 cPs). In these cases, it is usual to offer different diaphragm materials depending on whether the paint is water based or solvent based. In paint manufacturing industries 2″ and 3″ metal pumps are the most common. On the other hand, if paint is transferred within a factory, 1″ or 1 ½” pumps would be more suitable for the job. 3/8″ and ½” sized pumps are typically used in spraying equipment in paint booths.
Wastewater or waste oil applications: these applications are some of the most common uses for 1″ pump size as they are the most versatile size
Ceramic and mining applications: 2″ or 3″ pumps are usually used in these industries. They provide high flow rates, between 650 l/min (172 gal/min) and 1.000 l/min (264 gal/min). Their robust construction makes them perfect to confront the challenging conditions, such as highly viscous or abrasive materials, found in these harsh applications while providing maximum flow performance.
Chemical industry: depending on the flow rate needed any pump size may be suitable for these applications. Specialty chemical companies (or tollers) that modify the percentage concentration of base chemicals or make custom chemicals typically use pumps sized between 1″ and 2″. However, base chemical manufacturing usually has side processes in which, bigger pumps like 1 1/2″, 2″ or 3″ pumps are the most commonly used. Most common material combination for these industries is stainless steel or non-metallic pumps with PTFE diaphragms.
All things considered, AODD pumps versatile and reliable. Their adap is their most remarkable feature, them capable of pump a wide range almost any industry.
Source of Article