Hydraulic developments in the pump industry are hardly visible. Innovations are often focused on secondary matters, such as sensors for track and trace functionality.
In recent years, pump manufacturers mainly optimized production processes by minimalizing the costs for production. Reducing weight and thus material during the manufacturing process as well as purchasing (parts) in low-cost regions are examples we all know too well. Whether or not these activities led to improved product satisfaction for the users is another question.
In the past years, many small pump manufacturers have been taken over by the big players in the industry. This merging process is often accompanied by loss of whole product lines, as existing manufacturing locations already covered similar products. As time and/or interest to maintain the best of both worlds was nowhere to be found, product lines, which are not hydraulically or mechanically optimal, were maintained because of political reasons.
The focus of the world-leading companies was aimed at taking over the industry; real innovations and renewability were sources of expenses, rather than sources of income. Nowadays stock market values are leading, while developments with high investment costs and large yield time do not contribute to a rapid increase. Consequently, many years of product development are lost.
Although new (European) regulations have had an impact on developments in the designs of centrifugal pumps, it has become clear that hydraulic product and system knowledge is lacking at institutes composing these regulations. Guidelines are composed in such a way that interpretations, for better and worse, are possible. A product satisfying these regulations may, therefore, be a mile away from the intended results.
This can be demonstrated with an example, the DIN24255/EN733 water standard pump, which in recent years by most pump manufacturers has been upgraded to meet the higher efficiency requirements as described in the European Norm 16480. The idea of the regulations is to increase pump efficiency in order to increase sustainability. However, as only the pump efficiency is mentioned, rather than system efficiency, this has led to pumps in which the efficiency was increased by increasing the rated flow significantly resulting in very fluid velocities at the pump discharge. Velocities are as large as 15 ms-1 are often encountered in practice, whereas velocities in an order of magnitude of 5 ms-1 are desirable. Lower velocities are desirable in order to decrease excessive piping head losses and noise is favorable for maintenance reasons both for the pump and the system piping. Between a 15 and 5 ms-1 the difference in dynamic head that is contained in the fluid is equal to 10 m. For a pump that delivers 50 m head this means that 20% of the energy is still in very noisy and energy-consuming fluid velocity. For the pump with 5 ms-1 this would be only 2% of the overall energy (or head). To make pumps cheaper and easily meet the minimum efficiency index norm, instead of reducing the velocity within the pump, the fluid is slowed down by employing diffuser pipes, conical pipe pieces that have an increasing radius from the pump outlet to the system pipe diameter. The result is a significant pipe diffusion loss behind the pump and is not accounted for in the total cost of ownership (TCO).
As a result, these losses, and thus decrease of efficiency, is not found in specification sheets. These types of losses should be identified and included in the total efficiency by engineers with proper hydraulic knowledge, on top of pump and motor efficiencies. Only then a fair comparison between pumps can be made. Namely, when properly designing the hydraulics of such a pump, these diffusion losses are minimized within the volute (casing) and impeller (rotor) of the pump, such that a diffuser behind the pump is not required in order to reduce the fluid velocity.
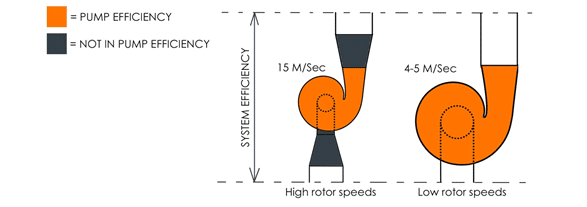
Figure 1 schematically illustrates the situation. Within the pump, diffusion losses are minimalized. Right after the pump, the pump efficiency is determined, which for a smaller pump (left) is slightly larger, compared to a larger pump (right). In order to achieve the same fluid velocity within the system, the fluid has to be slowed down behind the pump, in case of a smaller pump, resulting in large diffusion losses. This process is not required in case of a larger pump, and thus losses are negligible. This results in a system efficiency that is more favorable when a larger pump is in place, although the pump efficiency might initially be lower.
This small example illustrates the importance of hydraulic knowledge, both regarding the pump and system. Rodelta acknowledges this importance and spends a lot of effort in developing high-quality hydraulics; Rodelta’s distinctive vision. With this vision, Rodelta has developed a unique suction box for the OH5 API 610 pumps, which we think, has not been used in the market before. The suction box has a hydraulic shape and surface gradient that ensures that the flow lines take the bend in such a way that an optimally uniform inflow profile at the impeller eye is created. Our experienced hydraulic engineers have developed this solution through the use of Computational Fluid Dynamics (CFD) and organic shapes. A great example of hydraulic development, which also will be applied in other Rodelta product lines.
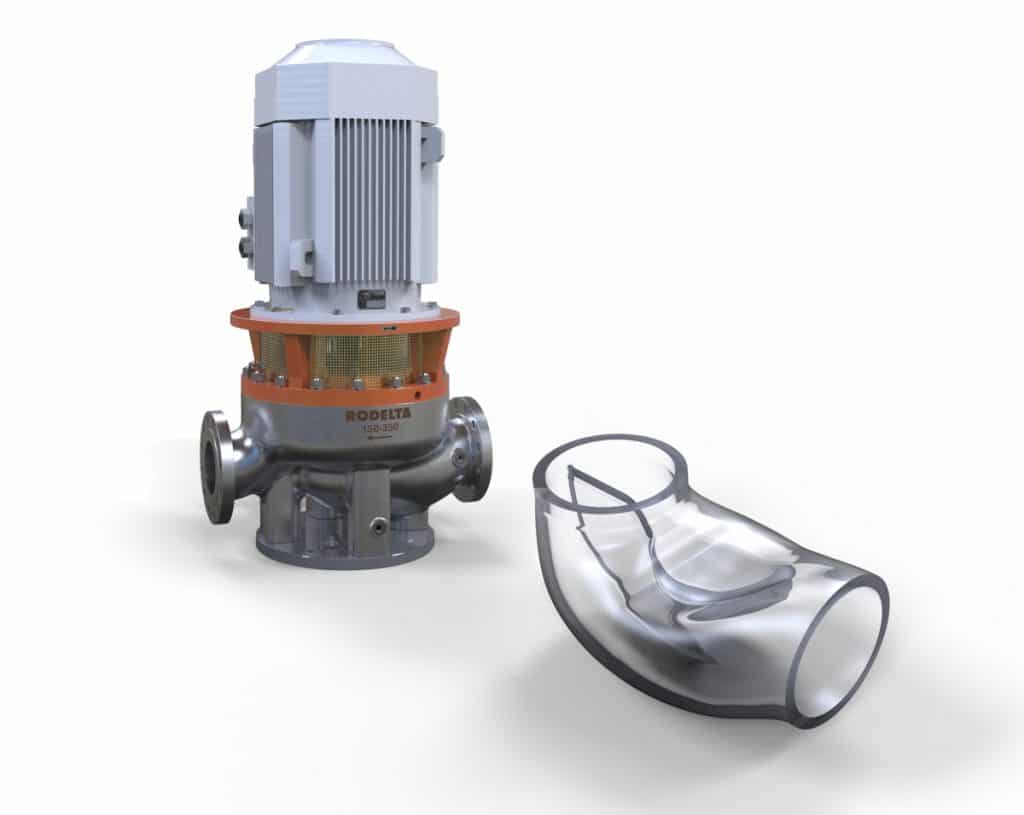
Furthermore Rodelta has the philosophy that each of their pump lines is designed in such a structured and refined way that for each customer required duty a pump can be selected running at or very near to the Best Efficiency Point. By combining a combination of several specific speed designs with a number of standard pumps sizes a flow and head field coverage of a complete duty range without overlapping designs is achieved as shown in Figure 3.
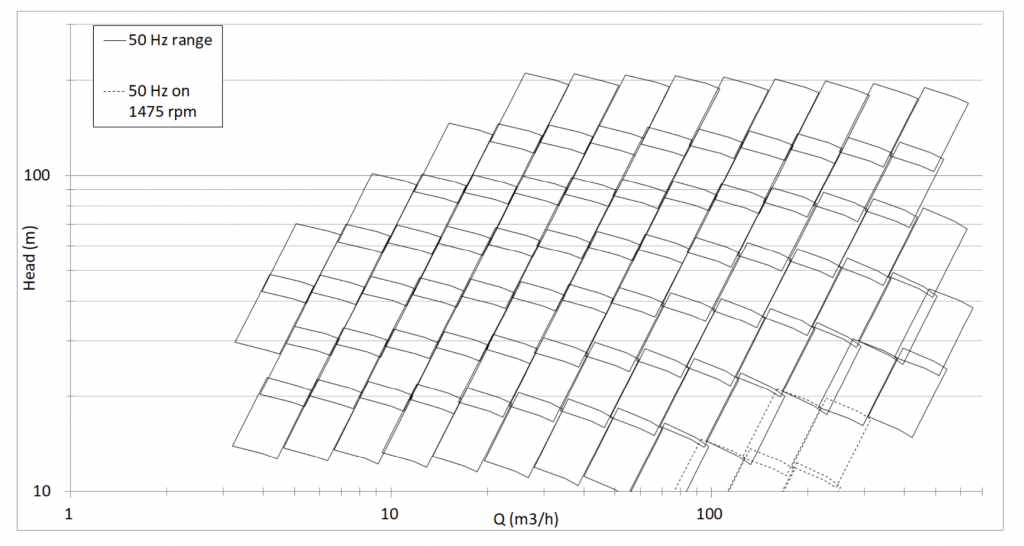
Within the available range, the required best efficiency point (BEP) can be exactly achieved by our custom diffuser technology. By designing and delivering customer-specific diffusers in each pump optimum pump efficiency at the desired duty will be obtained, completely in line with our vision while minimalizing emissions.
As Rodelta, we are often surprised to see how inefficient the hydraulic layout of pumping stations is designed. On the contrary the same buildings are often covered with solar collectors and plants in order to contribute to an ever-growing green environmental awareness. However, opportunities to contribute to a better environment by making a proper pump-system layout and matching pump selection are often not taken advantage of. Customers should realize that these possibilities can certainly lead to surprising results.
Click here for related articles and newsSearch for pump manufacturers in our equipment guide
Sign up for Pumps and Pumping Systems E-Updates
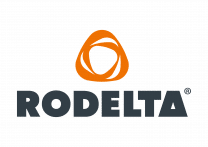
Rodelta Pumps International b.v. is a Dutch pump manufacturing company that is technology driven and market-oriented. We offer products for flood control, irrigation, drinking water, waste water, pulp & paper, power, chemical, oil & gas and general industries. Since 1946. The history of Rodelta In 1868 the family Stork started …
Source of Article