For the best part of 20 years, one of the UK’s leading glass bottle manufacturers had relied on the performance of four ageing split-case centrifugal pumps for the supply and circulation of process water throughout its plant.
However, by 2017 the pumps had started to display signs of declining performance due to excessive wear caused by the level of work demanded of them.
Over the years the pumps had become inefficient so in 2017 the decision was taken to look at how best to remedy the situation. Following a thorough inspection by Rotherham-based Industrial Pumps Ltd (IPL), it became clear that further repair work was going to be uneconomic. Based on the application details provided by the plant’s pump engineer and a review of the nature of the wear, IPL recommended in 2018 replacing all four pumps with two new KSB Omega pumps (Fig.1).
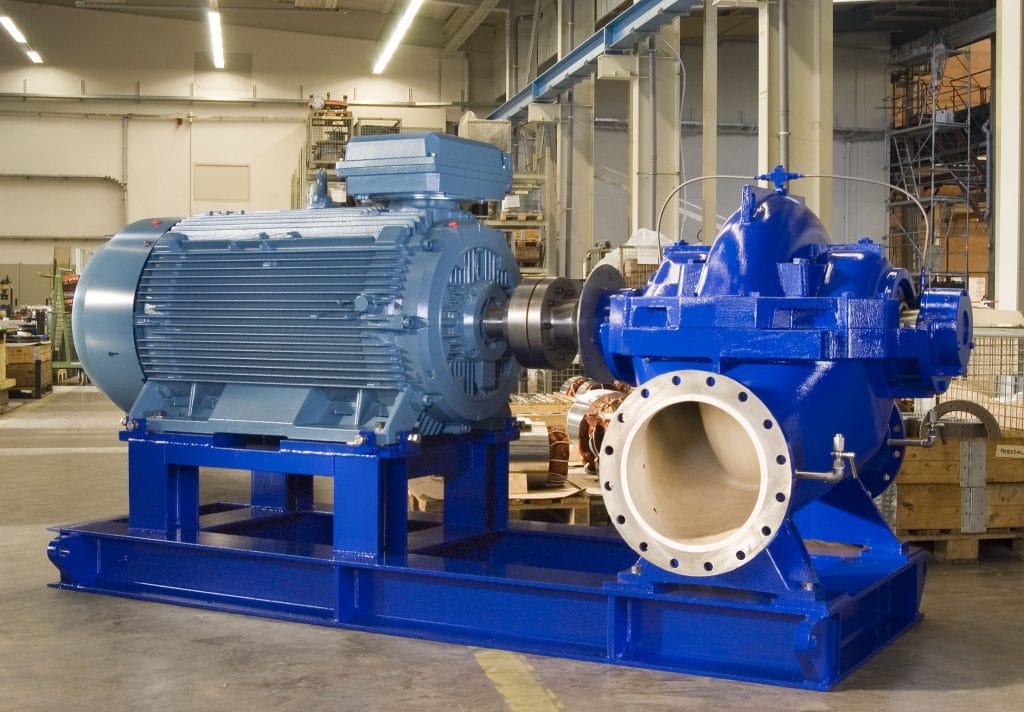
The process of manufacturing molten glass is continuous, with water drawn from two lagoons and pumped to the production areas where it is required. After passing through filtering weirs it is returned to the lagoons for re-use. Maintaining sufficient water in the lagoon and a flow of water at a controlled pressure is critical to the manufacturing process. Should there be a pump failure due to power cuts then the plant has to rely on towns water from the local water company. This is not only expensive, but the pipeline pressure is outside the company’s control may not be appropriate to the needs of the production.
Commenting on the process, David Silverwood, IPL Technical Sales Engineer says: “The water pumped contains quantities of glass, sand and various other solids and the cumulative effect of these aggressive particulates on the pump casings and other key components meant that it was uneconomical to effect repairs. In addition, it was becoming harder to source spare parts from the equipment manufacturer. A further consideration was the running costs of the pumps, which had escalated over time.”
The task facing IPL was to replace all four pumps with new units that would provide greater resistance to wear, deliver optimum performance at all times and reduce running costs. Following discussions with KSB UK Ltd, their answer was to install two KSB Omega 200-250 AGBV1 pumps in a duty/standby configuration. This would give the customer total control over the pumps in order to adjust flow levels in accordance with production requirements. The two Omega 200-250 AGBV1 pumps each delivering flows of 700m³/h at a head of 90m and power absorption of 206.7kw running at 1490rpm would be more than adequate to replace the four existing pumps. They would also be far more economical to run, with a reduction in the absorbed power being in excess of 50 percent.
KSB Omega pump
The axially-split, single stage volute casing Omega pump features a double entry radial impeller (Fig.2) and is ideally suited to the requirement of the water pumping stations as it provides the best duty point and gives operating efficiency levels of above 86%. The Omega’s double entry impeller compensates the axial forces so the load on the maintenance-free bearings is minimal. The combination of solid bearing brackets, a short and rigid shaft and pre-loaded bearings guarantees low vibration and extended operating life for the bearings, seals and coupling.
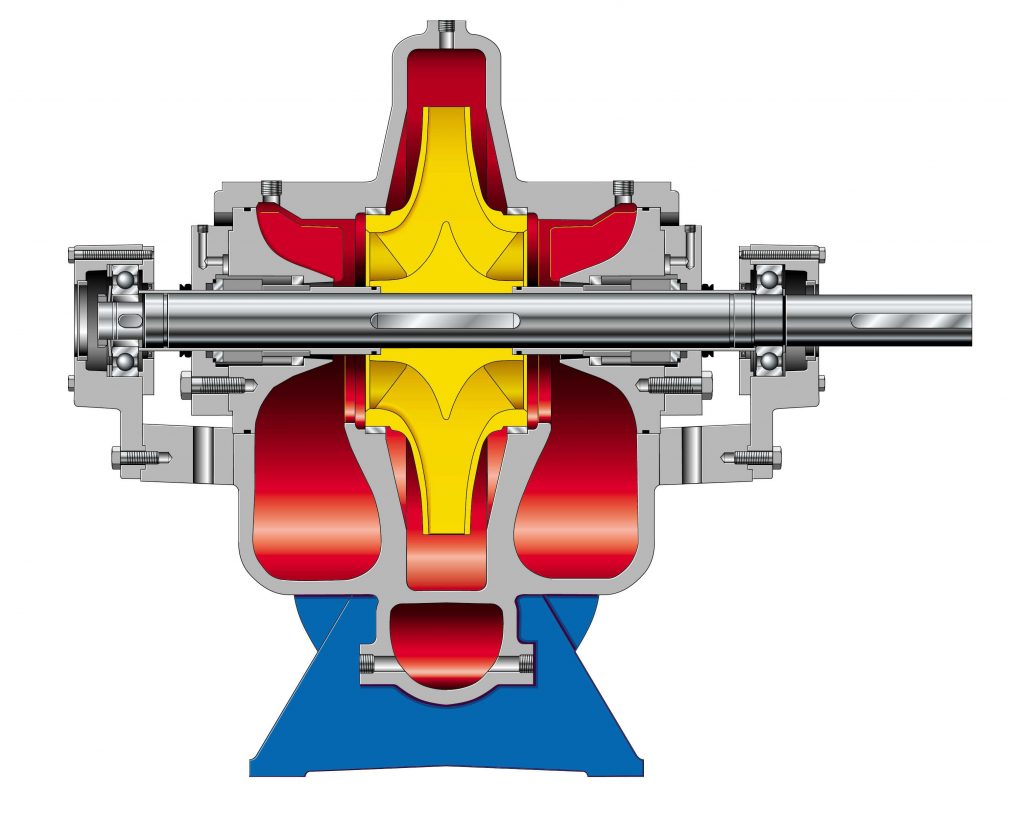
“The pump’s corrosion and abrasion resistant materials contribute to long service life by providing protection to key components,” explains Matthew Taylor, KSB UK Internal Sales Manager. “The axially-split case simplifies maintenance procedures, enabling ready access to all parts for thorough cleaning. The interior of the pump has been specifically designed to transport water with the minimum of flow resistance, a factor that also contributes to energy savings and reduced life-cycle costs.
“As with any project, capital investment costs are always closely examined at the outset and this was the case with our client,” continues David Silverwood. “After just 12 months of continuous operation our customer has been rewarded with power savings of 80kw/hr @ 0.7p/kw=£5.60 giving them a massive £49,000 reduction in the running costs of pumping water around the plant!.”
Click here for more informationClick here for related articles and newsSearch for pump manufacturers in our equipment guide
Sign up for Pumps and Pumping Systems E-Updates
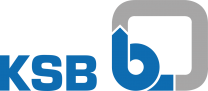
KSB is a leading supplier of pumps, valves and related systems.
These are used in a large variety of applications ranging from building services, industry and water transport to waste water treatment and power plant processes. Founded in Frankenthal, Germany, in 1871, the company has a presence on all continents with its own …
Source of Article