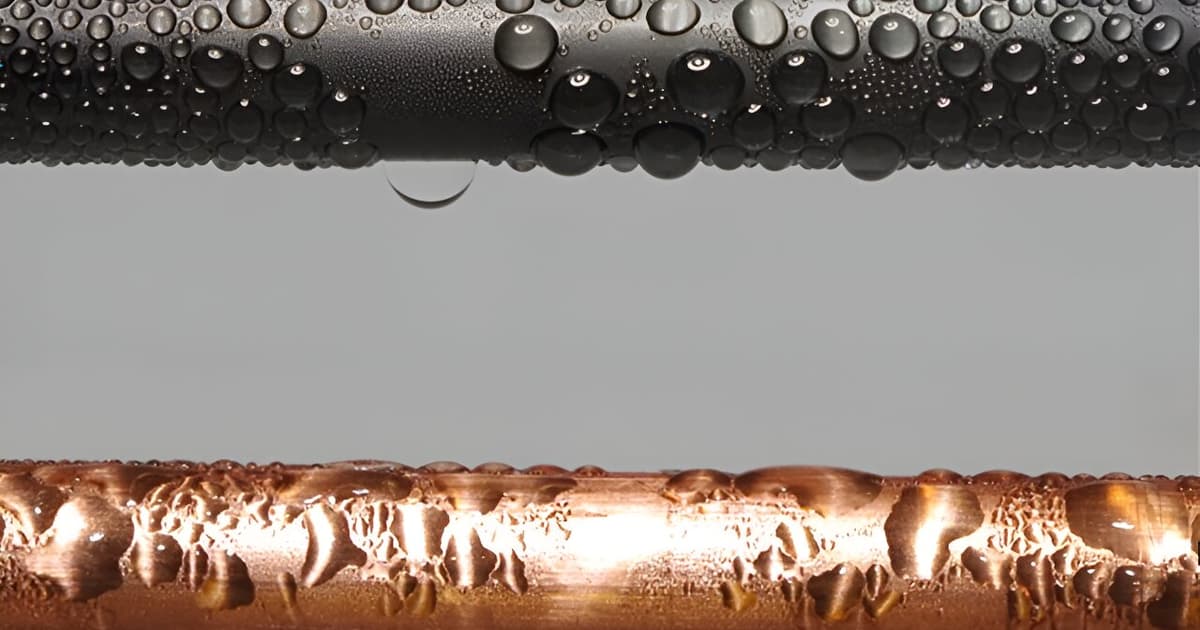
Weaning the world off fossil fuels will take some time, so finding ways to make energy generation more efficient is still important. Scientists at the University of Illinois Urbana-Champaign have developed a new coating for steam condenser pipes that, if rolled out widely, could potentially add more than a Russia’s worth of extra power per year.
Many types of power generation work on the steam cycle. Essentially, an energy source – whether that’s burning fossil fuels or through nuclear fission – is used to heat water in a boiler to produce steam, which is then channeled to spin a turbine, generating electricity. The steam is then collected in a condenser to reclaim the water to continue the cycle.
The researchers on the new study set out to improve the efficiency of the heat transfer of the condenser pipes. They developed a coating made of fluorinated diamond-like carbon (F-DLC), a material that’s hydrophobic, or water-repelling. When the steam condenses on the coated pipes, it no longer forms a thin film but balls up into droplets much more easily. That helps it run off faster, allowing more steam to come into contact with the pipe sooner.
In their tests, the team demonstrated that the coating boosted the pipe’s heat transfer properties by a factor of 20, which resulted in an overall efficiency boost of 2%. That might not sound like a whole lot, but according to their calculations, if all coal and natural gas power plants were 2% more efficient, then per year global CO2 emissions would drop by 460 million tons, 2 trillion gallons of cooling water would be saved, and an extra 1,000 TWh of electricity would be generated. That’s more than Russia consumes in a year.
“It’s remarkable that we can achieve this with F-DLC, something that just uses carbon, fluorene and a little bit of silicon,” said Muhammad Hoque, lead author of the study. “And it can coat pretty much any common metal, including copper, bronze, aluminum and titanium.”
Importantly, the coatings were durability tested for 1,095 days, and found that they maintained their function for the whole time. They also did so after being scratched 5,000 times in an abrasion test.
The next step, the team says, is to test the coating’s performance under real-world industrial conditions for six months. While there are still questions of how such a coating might be put into wide use, even just a few plants adopting it should start to make a difference. Similar coatings have been made of materials like graphene, with similar results.
“If all goes well, we hope to show everyone that this is an effective solution that is economically viable,” said Nenad Miljkovic, lead researcher on the project. “We want our solution to be adopted, because, although the development of renewable energy should absolutely be a priority, it’s still very worthwhile to continue improving what we have now.”
The research was published in the journal Nature Communications.
Source: University of Illinois Urbana-Champaign
Source of Article