For chemical plants, chemical tank farms and refineries, atmospheric corrosion of steel is a continual concern that can require re-priming and re-painting every few years to prevent safety issues and the premature replacement of costly infrastructure.
Industrial primers represent a critical foundation for paints and coatings in harsh environments. However, they have certain limitations and have historically been unable to effectively deal with the eventual formation and future recurrence of rust. Traditional primers only encapsulate rust until the paint/primer is scratched, chipped, or breached and moisture and oxygen migrate under the film, allowing the corrosion to spread.
As a result, facility maintenance personnel or contracted coating applicators must repeatedly utilize costly, time-consuming and environmentally hazardous surface preparation methods such as sandblasting to prepare surfaces to be primed and repainted. However, not all environments can withstand the impact of sandblasting, which can damage critical surfaces and may be impractical for reaching hard-to-access areas such as cracks and crevices. Sandblasting is also expensive and time-consuming, and even poses its own safety risks to applicators and the environment.
Now, however, more advanced primers have been formulated that set a higher performance bar in corrosive environments. These reactive primers go beyond encapsulating rust to instead convert it to a protective material (iron phosphate) to minimize the risk of further corrosion. The chemical bond provides superior adhesion, high corrosion protection and also eliminates under-film corrosion.
The rust conversion formulation also differs from prior technologies by using a non-toxic, ultra-low VOC water-based acrylic polymer solution that can be applied with minimal surface preparation and without the need for sandblasting of steel substrates.
Primer Pitfalls Allow Corrosion
One of the main reasons that petrochemical facilities are so susceptible to corrosion is that traditional primers have serious deficiencies in this area.
“We have found that the typical primer and topcoat needs to be replaced in a harsh chemical facility environment every couple of years,” says Dave Marzano, owner of Maxim Contracting, a Newark, New Jersey-based industrial and commercial contractor.
“There are not many products out there that will stop the rust.”
A common failure of primers is not sufficiently protecting against under-film corrosion.
“A primer must first form an effective chemical bond to the metal substrate,” says Martin Lawrence, Managing Director of New Jersey-based NanoRustX LLC, a supplier of advanced primer technologies. “Without this, rust promoters like oxygen and humidity will creep underneath the primer causing further corrosion. Most primers on the market go only as far as encapsulating the iron oxide which is not 100% effective in preventing further rust from occurring.”
Another reason that chemical facilities are prone to corrosion when utilizing typical primers is that a high level of surface preparation is required because most rust primers on the market are sensitive to chlorides.
“Even a minute amount of chloride on the steel can cause coating system failure,” says Lawrence. “This is why leading coating manufacturers demand extreme levels of surface cleaning (sandblasting) and removal of chlorides to a level of 5 mcgr/m2, which is nearly impossible to achieve. Even when sandblasting is used for surface preparation, flash rusting will still occur.”
In response, the search for more enduring corrosion protection at petrochemical facilities has involved the development of long-lasting primers that correct the deficiencies of traditional methods.
Lasting Corrosion Protection
NanoRustX (NRX) NanoPrime, for example, works by chemically reacting with iron and iron oxide (rust) to form iron phosphate and creates a Nano bond with both metallic and painted surfaces. The chemically bonded layer is insoluble and extremely corrosion resistant. This “bonding” process also provides superior adhesion and flexibility and stops under-film corrosion that occurs when conventional coatings are damaged.
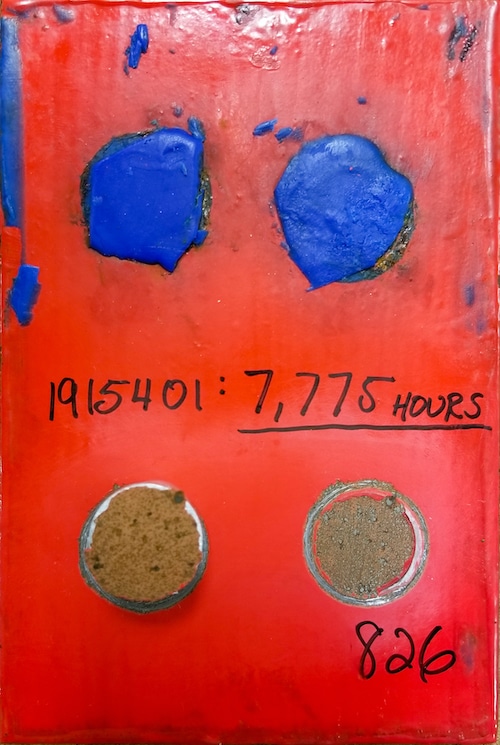
The non-toxic, ultra-low VOC primer contains nano-polymers for added strength and durability and has been tested to successfully coat surfaces from rust-free to up to 700 microns of rust. The elasticity of the advanced primer makes it very durable in temperature variations from -670C to +2000C (-900F to 400F).
Because the advanced primer actually chemically reacts with galvanized steel surface, no surface preparation is required other than a water wash. The water-based acrylic polymer is not sensitive to chlorides or rust and can actually neutralize them. Unlike initial generations of rust converting primers, the primer performs equally well on clean, partially corroded and heavily rusted surfaces. Typically, a power wash (240 bar/3500 psi) is all that is needed before applying to steel (clean or corroded), galvanized steel or aluminum in order to remove loose paint, dirt and grease. The primer can be applied to a corroded surface by hand brush, roller or airless spray gun on the substrate. After the application of the primer, a single coat of a low VOC top coat will complete the job.
When a chemical plant in the Newark, New Jersey area had a number of roof exhausts with severe corrosion, Marzano, who had sought a lasting corrosion solution for his customers, applied a coat of NRX NanoPrime with no topcoat to a 50’ high roof stack as a trial.
“The roof exhausts were so rusty the chemical company was ready to replace them, which would have cost about $7,000 to 9,000,” says Marzano. “However, about five years later there still is no visible rust on the roof exhausts. The success of the trial demonstrated the primer’s effectiveness against chemical plant corrosion, so we have applied it many times since then on everything from roofs, exhaust fans, and exhaust stacks to tanks for carbon monoxide and sulphuric acid.”
In one of Marzano’s recent applications, his Maxim Contracting work crew coated four outdoor and three indoor chemical tanks, ranging from 1,500-10,000 gallons, including a liquid nitrogen tank and a 2,000-gallon CO2 tank.
Using a spackle knife and palm sander to remove existing loose flaking paint and rust, and a water wash with nearby hose, the surfaces were readied for applying the primer. The system included two coatings of primer applied by roller, followed by one application of the customer supplied water-based, industrial epoxy topcoat.
“With NRX NanoPrime, less surface preparation is required compared to other primers,” says Marzano. “Also, it can dry in 30 minutes to touch and takes about two hours to apply a second coat, depending on temperature, which is much faster than typical primer and paint. So, we finished the job in a few days rather than a week, which helped to reduce potential downtime for the facility.”
“But the bottom line is that the primer prevents corrosion and really lasts,” concludes Marzano.
For more information on NRX NanoPrime, please visit www.nanorustx.com, email sales@nanorustx.com or call 1-973-751-2200.
Sign up for Fluid Storage E-Updates
Source of Article