Imagine if there were a metallic device that could be transported all squished down into a compact ball, but that would automatically “bloom” out into its useful form when heated. Well, that may soon be possible, thanks to a newly developed liquid metal lattice.
Led by Asst. Prof. Pu Zhang, a team of scientists at New York’s Bingham University started by 3D printing lattice-type structures out of an existing metal known as Field’s alloy. Named after its inventor, chemist Simon Quellen Field, the alloy consists of a mixture of bismuth, indium and tin. It also melts when heated to just 62° C (144° F), but then re-solidifies upon cooling.
Utilizing a combination of vacuum casting and a technique known as conformal coating, those alloy lattices were subsequently covered with a layer of rubber. As long as the ambient temperature stayed below 62 degrees, the resulting structures remained rigid.
Once heated above that point, however, the alloy melted, but was still contained within the rubber shell. In this malleable form, the structures could then be pressed flat or otherwise deformed. If they were held in that form while the alloy subsequently cooled and re-hardened, they would retain that altered shape indefinitely.
Upon being reheated to over 62, though, the alloy once again melted. In the same way that a rubber toy pops back into its original shape after being squished down, the lattices’ rubber shells were then likewise able to return to their original shape, pulling the liquid metal into place along with them. Once they cooled, the alloy hardened again into its “proper” shape.
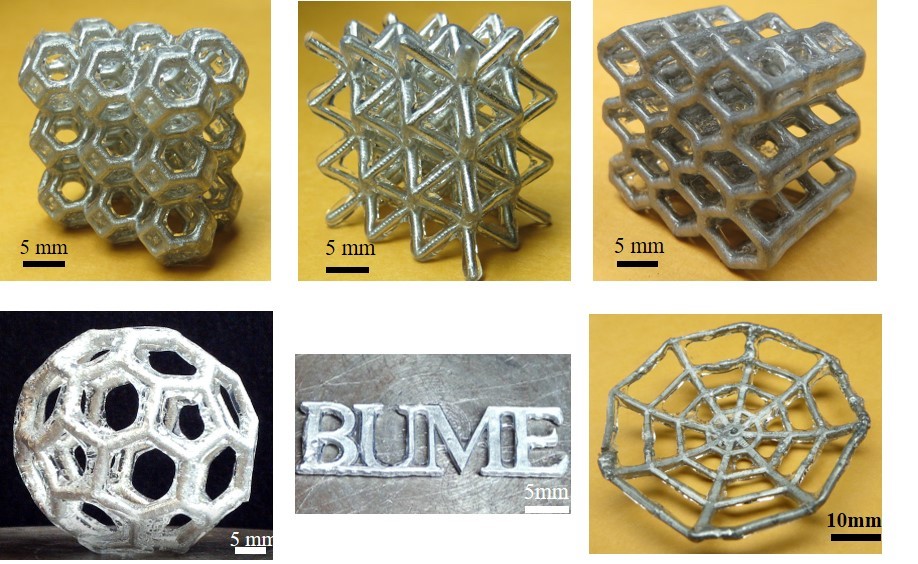
Pu Zhang
So far, the team has used the technology to create items such as spider web-like mesh antennas, soccer balls, honeycombs, an even a Terminator 2-like hand that opens up as the alloy melts. The lattice might conceivably also be utilized in applications such as the landing gear for spacecraft, which could absorb crash energy by buckling, but then return to their original shape after being heated and cooled.
“Normally, engineers use aluminum or steel to produce the cushion structures, but after you land on the moon, the metal absorbs the energy and deforms. It’s over – you can use it only once,” says Zhang. “Using this Field’s alloy, you can crash into it like other metals, but then heat it up later to recover its shape. You can use it over and over again.”
The research is described in a paper that was recently published in the journal Additive Manufacturing.
Source: Bingham University via EurekAlert
Source of Article