Wastewater Compliance Monitoring
Due to increasing water scarcity, the requirements for trade effluent discharge consent and rising cost of trade effluent disposal, plant owners are seeking ways to reduce the cost of wastewater disposal and as part of working towards becoming carbon neutral, monitoring waste output and how it can be reduced.
Wastewater compliance monitoring and sampling involves the taking of small samples of wastewater and testing for the presence of harmful contaminants, Biochemical Oxygen Demand (BOD) levels and presence of Dissolved Oxygen to prevent harmful wastewater entering the surrounding ecosystem and damaging the local population, plant, or wildlife. Regular sampling and a proactive approach allow problems to be caught early minimising long-term damage.
In addition to social and ethical reasons for monitoring, there can be hefty fines if rules are broken and industrial plants are found to have discharged trade effluent at levels above, they have consent for, and outside agreed quality limits polluting the surrounding area. There are strict guidelines to follow, however there are also huge benefits for the plant owners from monitoring in the form of protecting profits.
Sampling waste also allows operators to detect process leaks and trace its origin early before there are large losses in revenue. For example, it is possible for high value process liquids such as chemicals, juices, milk, or colourings to enter waste flows through valve leaks, pipework leaks or overflowing of vessels. Detecting this early and reacting not only protects the environment but also protects profits, a big incentive to regularly monitor waste streams.
A pump is required to extract the water for sampling, quite often the samples required are small meaning specialist dosing pumps are needed. It can be difficult to accurately select a pump for these applications as contaminants are unknown, sometimes forming viscous abrasive sludges or leading to high amounts of dry solids content therefore causing clogging or dry running. If a wastewater producer is involved in metal processing, it is essential any pump involved in monitoring is free of metal so as not to interfere with readings from the process medium.
It is common for the pump to be situated above the water surface where levels can change, therefore requiring a self-priming pump. The complicated conditions and variation in water quality often necessitates costly protection devices for the unit installed, these are not always 100% effective and the sophisticated pump designs can lead to expensive part costs and large maintenance bills as they can also be difficult to maintain.
Continuous Remote Wastewater Monitoring Design
This project involved supplying remote sampling pumps for 24/7 monitoring across 15 different sites in the UK. The customer samples dirty water and has experienced issues with other pump technologies due to low water levels causing dry running. In addition to this, there are other complications such as fluctuating inlet pressures and various types of solids including twigs, grass, and mud.
The client preferred a low maintenance and reliable pump solution due to the remote location of the pumps. They required the units to self-prime, handle solids without clogging and be quick and low cost to maintain in the event of a failure. The units operate at around 500L/hr at low pressures and are controlled remotely across the various testing locations, while away from site they need to be able to alter the speed, monitor the pump condition and reverse the flow in the event of clogging.

Our Low Maintenance, Continuous Sampling Pumps
We specified 14 qty AMP 16 peristaltic pumps for this project as they provide all the benefits this customer requires. They are consistently reliable in slurry, sludge and wastewater applications while also being simple and cost effective to maintain.
Peristaltic pumps, also known as hose pumps, are simple in design as there is only one wearing internal part, the hose. This is easily and quickly replaced without the requirement of special training or tools; this is an excellent benefit for 24/7 remote applications such as this where excess amounts of downtime cannot be tolerated and where often only low skilled staff are available to perform urgent repairs.
Being simple to maintain does not detract from their dependability and robustness, the absence of mechanical seals allows the pump to run dry indefinitely without damage. Operating at low speeds with the peristalsis pumping action facilitates self-priming and the handling of viscous fluids without issues. As the unit can run dry it also guarantees sample quality as the pump can be completely emptied of fluid before the next sample is taken preventing cross contamination.
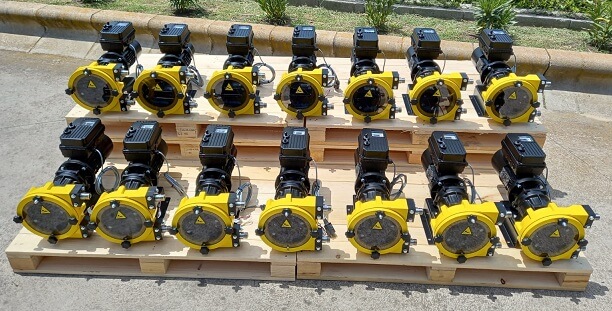
Peristaltic Pump Benefits over Traditional Positive Displacement Pumps
The absence of valves and seals means that solids up to the size of the internal diameter of the hose can be passed without clogging, in addition to this the gentle pumping action does not alter the state of shear sensitive fluids or damage delicate solid particles. In the unlikely event of clogging, the unit is reversible meaning the pump can be unclogged by simply reversing the flow, another big benefit for this customer remotely operating across so many sites.
Peristaltic pumps have all the benefits of positive displacement pumps with few of the weaknesses, their operation is slip free meaning they can handle both thin and viscous fluids without losses in efficiency, other pump designs can experience slippage with varying viscosities that can lead to differing performances.
We installed all the pumps with hose leakage detectors to reduce plant downtime as much as possible, this is a particularly useful feature for the client as it sends a signal to a control panel if the internal hose ruptures. The engineers then know immediately that the hose needs replacing, and they can act on it quickly and have the unit up and running straight away.
The internal hose is available in differing materials to accommodate a wide range of chemicals, a particularly useful feature for these processes as all possible contaminants cannot be unknown upfront. This allows the client to purchase a different hose material in the future should chemicals enter the flow stream that are incompatible with the currently installed material.
The modern roller design increases efficiency and reduces power consumption by up to 30% compared to other traditional peristaltic pump designs, this also leads to increased hose life and even with 24/7 operation the sites can expect years of trouble-free operation with maintenance and lubrication intervals as far as 12 months apart.
After trialling our AMP 16 pump the customer was convinced and ordered an additional 14 units complete with single phase inverter, hose leakage detector and forced air cooling for operating the motor at very slow speeds when extremely low flow rates are required. This unit facilitates a wide range of flow rates by simply altering the speed, a truly reliable and flexible pump solution for their sampling systems.
Source of Article