Precisely managing the flow of liquids and gases requires actuators to control the valves. Actuators play a critical role, and service engineers from Rotork are available to repair actuators if issues should arise. However, for most companies, the best solution is to prevent faults and shutdowns from happening proactively in the first place.
At the Pengerang Deepwater Petroleum Terminal in Malaysia, hundreds of intelligent electric actuators control the flow of liquids and gases. The terminal relies on precise electric actuation to ensure safe and efficient operations while limiting environmental impact. Rotork Site Services (RSS) provides field support at Pengerang for repairs, commissioning, upgrades, and maintenance. It’s part of a maintenance offering to customers that ranges from basic repairs to a premium package for actuators on critical processes.
Tiered maintenance and data-driven analytics
Rotork experts work with a site to determine which actuators control the most critical processes within a plant. It might be just a handful, so a tiered maintenance approach makes sense. Companies can opt for a premium package for actuators to control their most critical processes and choose one of the other levels for less hazardous situations.
With the basic package, engineers visit a site to inspect the actuators. With the premium offering, they visit more frequently, thoroughly investigating each actuator and changing seals, oil, and parts as necessary.
An intelligent asset management system, like Rotork’s iAM, collects data logs from intelligent actuators, such as Rotork’s IQ3 Pro range. The data collected includes vibration, temperature, torque, number of starts and whether the unit has lost power.
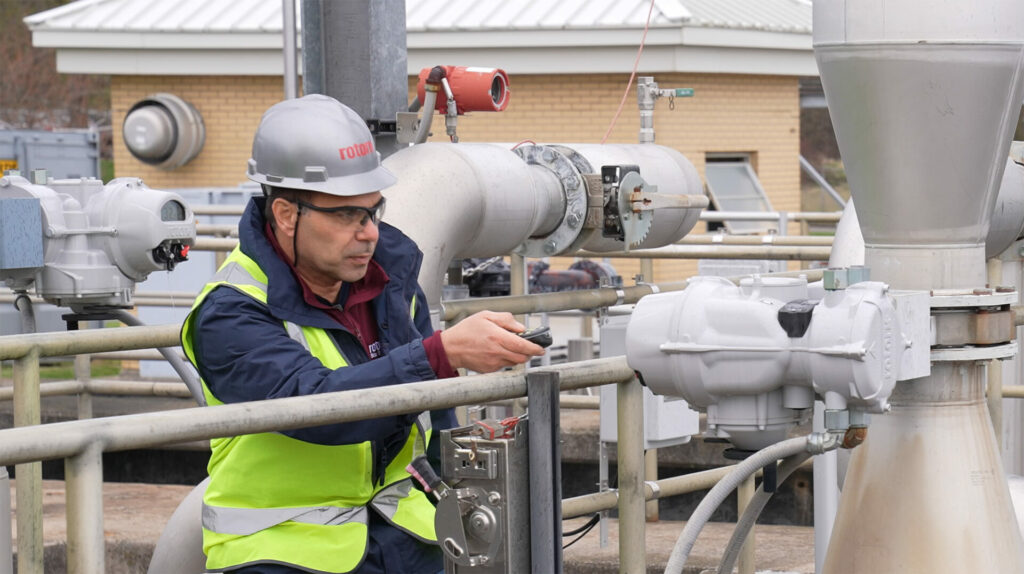
This data is fed into an algorithm which enables Rotork experts to assess an actuator’s health and make maintenance recommendations, helping to increase uptime.
Intelligent electric actuators can enhance safety, efficiency, and environmental performance, but regular maintenance is key. Specialist systems can analyse data logs from intelligent actuators to assist with appropriate maintenance actions, ensuring optimum performance, reduced costs and minimised risk to the plant.
Any maintenance plan must consider the user’s needs to be truly effective. Being proactive with maintenance and using advanced data can reduce unplanned downtime and enhance safety and efficiency for end users.
Source of Article