The timer has started. By 2050, the UK has a target of Net Zero Emissions meaning any emissions generated must be balanced by schemes offsetting an equivalent amount of gas emitted.
This could be performed through carbon offsetting programs, but ideally companies are looking to reduce, reuse or recycle more to meet these objectives sooner before carbon pricing comes into force.
But how can companies work towards achieving Net Zero with pumps?
Reduce
One method to reduce pump related carbon emissions is to reduce the power consumed, decrease the amount of wastage, lubricants spent, and spare parts consumed by the unit during operation.
In order to do this we need to look at becoming more efficient which is fairly easy if we are talking about one pump or application, but across a number of applications and with liquids varying according to what the process demands, it quickly becomes more complicated.
Working with a partner who is not restricted to a single pump technology ensures the correct technology is utilized guaranteeing longevity. Often a pumping application can performed by a variety of pump types and working with a partner who can way up the advantages and disadvantages of the various types, and are transparent in their selection ensures the right pump for your process is supplied from the outset.
Reuse – Recycled or Dry Fluids
Another way to reduce the carbon footprint of companies undertaking processes such as jet washing, hydro demolition, paint, plastic or rubber removal from metal components for recycling, is to evaluate whether fluid recycling or reuse can be implemented.
Historically high-pressure jets of water are used to remove layers involving the pumping of fresh clean water, with water which has been spent, drained away or disposed of.
Pump designs are available which utilize recycled water enabling jetting fluids to be recycled and recirculated within the pump head vastly reducing water use. A device such as the North Ridge Hull Cleaner which can be adapted for similar processes, does not utilise grit or other media to remove coatings. Hydro-blasting also eliminates the costly use of sand or grit – the worlds’ second most consumed natural resource, is quieter, and ensures rebar is not damaged enabling its reuse.
Hydro-blasting is far more efficient too covering up to 30-40 square metres an hour as opposed to sand blasting using traditional methods which can only cover up to 10sqm an hour.
Recycle – Creating Energy in place of Pressure Reducing Valves
High pressures can often harm equipment further downstream from process or for safety reasons be undesirable if there is risk of pipeline equipment failure lead to fluid escape. Excess pressure in a pipeline is often wasted.
Excess pressure is reduced within process via the utilization of pressure reducing valves. Such valves reduce pressure with excess energy being left unused.
Using a Pump as Turbine enables this otherwise wasted excess energy to be converted into energy. The unit runs in reverse rotating a generator as the impeller rotates from excess flow and pressure. Unlike turbines, the payback can be as little as 2-5 years, and their uncomplicated design enables maintenance to be performed without special tools, knowledge or expertise. The unit can also function as a pump if required.
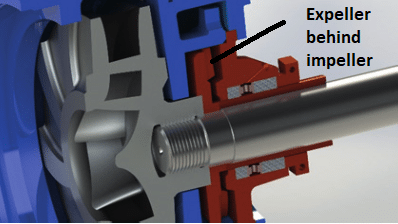
Here are 14 Checks you can make within your plant today:
- Excessive throttling of pumps by valves.
- Continuous use of bypass lines leading to excessive amounts of fluid recirculation
- Frequent spare part replacement of bearings, mechanical seals, and gaskets.
- Cavitation with pumps operating noisily and consuming higher power than required.
- Check Wear Ring Clearances. A 50% decrease in wear ring clearance can increase efficiency between 2-4% and reduce the risk of cavitation
- Oversized pumps with units being frequently operated away from duty point.
- Pumps with IE1 / IE2 Motors running continuously. Utilising a pump with a VFD can reduce energy consumption by up to 50%.
- Checking for Air Leaks which can lead to savings of between 20-50%
- Check whether heating of fluids will enable easier and lower energy methods of transfer, reduce pump wear and increase recovery rates from containers.
- Check whether containers are being returned to suppliers which are still partially filled.
- Check whether pumps operating in Parallel are utilizing inverters and appropriate technology to meet the required duty points against the system curve, or if one pump is in operation whether a second in parallel will improve pumping efficiency reducing overall power consumption.
- Check pipework is sized correctly and renewed periodically to keep friction losses at a minimum.
- If pump maintenance is reactive rather than proactive leading to downtime, and product wastage. Check whether the 6 to 1 rule is being followed.
- Use of Pressure reducing valves where a pump as turbine can be used for energy recovery.
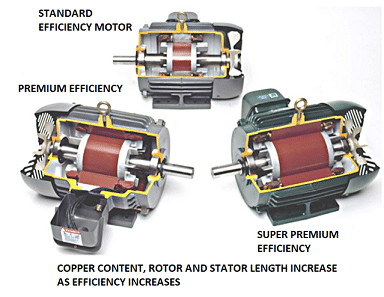
Click here for related articles and newsSearch for pump manufacturers in our equipment guide
Sign up for Pumps and Pumping Systems E-Updates

North Ridge Pumps are a manufacturer and distributor of a wide range of pumps to cover most applications. Our ranges include; centrifugal, multistage, vane, peristaltic, screw, gear, air operated diaphragm, vertical immersion, submersible, barrel, flexible impeller and side channel. Our pumps are available in cast iron, stainless steel 304, stainless …
Source of Article