Maintaining complex systems in the OEM industry can oftentimes be a challenge, particularly when something goes wrong that causes automatic systems to leak.
This not only creates burdensome operational downtime, it drains economic resources — lost time means lost money. Historically OEMs have relied on control valves that are pneumatically actuated. But these systems have their drawbacks even when they do not require costly maintenance, with lags in fluctuation response time and hazards that are built into the pneumatic technology itself.
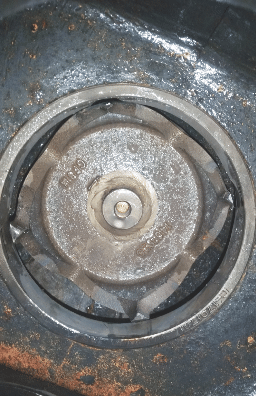
A standard pneumatic actuator modulating valve control will generally only spend 20 percent of the time actually moving and modulating– sitting idle 80 percent of the time. In many application contexts, such as large corporate campuses, universities, and military bases, that require high temperature hot water systems a higher amount of energy expenditure is required to prevent overheated water. The implication here is that pneumatic systems require greater operational oversight to mitigate these risks manually. Greater oversight means both greater costs and a greater amount of labor time that could deviate from other urgent tasks.
Moreover, pneumatic actuators are highly sensitive to environmental factors including shock forces that many plant operators may be unaware of. For example, pneumatic actuators are vulnerable to shock forces that can occur from water hammer and piping systems, even steam piping systems. The velocity of steam can move at 70 miles an hour down a pipe and can slam right into a valve: if that valve is controlled with a plastic spindle, the pressure can cause an unintended break and likely leak into the system. When this happens, the maintenance costs rack up very quickly.
Electric Actuation: New Advances, New Solutions
For end users, these perils and costs associated with traditional actuators have always been a necessary compromise that comes with the technology itself. But the industry is starting to take notice of new solutions, particularly with respect to electric actuation. One problem, however, that has stalled this emerging market has been to develop electric solutions that retain some of the full advantages of pneumatic or hydraulic actuation — namely, operational speed and consistency. Early electric solutions lacked the precision and responsiveness of pneumatic or hydraulic systems in controlling and regulating the force and speed. Moreover, while pneumatic systems carry a significantly higher operational cost than electric, the component costs for pneumatic systems have been lower. Traditional electric actuators carry risks of their own, as well, from overheating to moisture sensitivity.
To solve common challenges, the industry standard is rapidly moving towards electrically actuated, modulating globe control valves. The mission is to provide an instrument suited for challenging, modulating, industrial processes that require electric actuation with the actuation speed and solid reliability of pneumatics. Advances in the industry have allowed for the development of new technology has allowed us to move beyond these traditional limitations of electric actuation while retaining its significant cost-effective advantages.
Warren Controls, a leading manufacturer of control valves and specialty fluid handling products, has taken a noteworthy step forward in the market for novel actuation solutions with their ARIA Series of electrically actuated, modulating, globe control valves. Warren Controls entered into a research and development initiative spanning several years, specifically to resolve issues faced by the steam fired instantaneous water heater markets.
The valves are ideally suited for challenging, modulating, industrial processes that require electric actuation with the actuation speed and reliability of pneumatics. The new ARIA series is an upgraded version of Warren Controls’ AmurAct. The newly improved actuator is designed for 1.5 million cycles and can withstand ambient temperatures up to 150 degrees Fahrenheit, with travel speeds at 12 seconds per inch (nine seconds for ¾-inch stroke valves). ARIA is equipped with an electric spring fail safe (when opened or closed), robust enclosures with IP67 / NEMA 4X enclosure and water tight ½” NPT fittings, and has split range input capability for 1/3-2/3 high/low applications.
Engineering Integrity for the End User
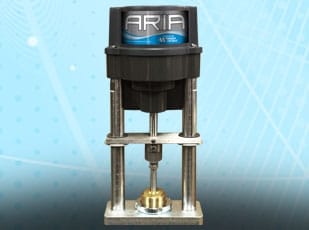
This solves a number of problems for users, and Warren Controls created the ARIA Series with customers in mind. It’s designed for 1.5 million cycles, and of course includes all common control and feedback systems. Four valve series are available with the ARIA actuator for customized use: the ARA is a three-way cast flanged steel valve for 1/2” – 2”; the ARB is a two-way or three-way threaded bronze or stainless steel valve for 1/2” – 2”; The ARC is a two-way or three-way flanged cast iron valve for 2-1/2” – 6”; and the ARD is a two-way flanged steel cage valve for 1/2” – 2.” The ARIA electric actuator has a NEMA 4x rating with a capability of withstanding ambient temperatures up to 150°F. This means ARIA could survive a really hot control room, and it also has very good resolution. It has an internal feedback mechanism for the linear stroke of 12 bits or 4000 parts of resolution. The advanced features like galvanic isolation between the inputs and the outputs means user systems don’t end up with ground-loop problems when contecting to PLCs (programmable logic controllers) and other central control systems.
Customers in the district/campus energy sector, or those working source-side HVAC systems, where high temperature, hot water applications are in use (like a colleges/universities or military bases), will benefit from the ARA or ARD. The ARB and ARC are ideal for those in the food and beverage industry to control steam and water applications. Going with a high-resolution electric actuator means the controlled flow is adjusted very tightly to the flow requirement, unlike an HVAC actuator. HVAC actuators might only have 100 parts of resolution for full valve stroke, so it moves in 1 percent increments whereas high-resolution electric actuators move in a tenth of a percent increments.
The Warren Controls family of products bridges the gap between industrial, HVAC and district/ campus energy. Its “Product Builder” philosophy allows unique and specific engineered configurations to be created quickly, with timely checks and no delays. This translates into much shorter lead times than industry standards for similar products.
Written by Al Gunnarson, VP of Sales and Marketing Warren Controls, Inc.
About the author:
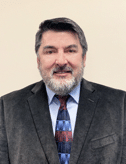
Albert H. Gunnarson is the Vice President of Sales, Marketing & Product Development at Warren Controls, where he leads, trains and develops the essential materials and new projects needed in the Warren Controls product line. Albert has a BSEET from DeVry Institute of Technology and an MBA from The Lake Forest Graduate School of Management. He has been designing, specifying, applying and marketing control systems and control valves for more than 35 years. In his passion for educating customers in control valve design and proper valve selection, he co-created Warren Controls’ popular Valve Sizing & Selection program, ValveWorks®.
Click here for more informationClick here for related articles and newsSearch for Valve manufacturers in our equipment guide
Sign up for Process and Control Valves E-Updates
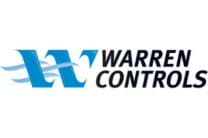
Warren Controls is an industry leader in Industrial Control Valves, Building Automation Valves, Deaerator and Boiler Level Controls, and Military/Marine Valves. For more than 70 years, the company has maintained a strong commitment to providing specialty alloys, quick deliveries, and knowledgeable customer service. Warren Controls has earned a sterling …
Source of Article