Dongducheon Combined Cycle Power Plant (CCPP) is one of the largest CCPPs in South Korea having a power production capacity of 1,716MW (858MW x 2 Units). The plant consists of 4 gas turbines + 2 steam turbines and generators supplied by MHI (Mitsubishi Heavy Industries Ltd) and the 6 BFW pumps supplied by Hyosung Goodsprings.
Ever since the commissioning stage of the plant in 2015, the plant has faced serious cavitation problems in the AR Valves protecting the pumps because the ARVs are often operated under extremely critical operating conditions. Plant operation logic and TCA Cooler operations require low flow rates below pump minimum flow, which makes the AR Valves operate at partial-load and quite often daily startup/shutdown operation.
The main reason for cavitation was the – at times – very low flow rate and thus critical load condition of the valves. Low flow rates often cause cavitation in AR Valves.
In the current plant concept, which today is common for most CCPPs, each of the 3 boiler feed pumps (per steam turbine) has the capacity to provide the full rated flow of the HRSG-drum. This is one of the critical load cases which led to the damage in the AR Valves installed then.
To cool the turbine, feed water is supplied to a TCA cooler (Turbine Cooling Air). In this heat exchanger, the cooling air for the gas turbine transfers its heat to the boiler feed water. The TCA cooler is not to be confused with the HRSG – its purpose is to cool the gas turbine unit, not to generate steam. This cooling flow is also significantly lower than the minimum pump flow and again this results in critical case of partial-load operation which can generate heavy cavitation on the internal parts of the ARV bypass branch, especially under a high-pressure application of 218 bar differential pressure at Qmin.
When the bypass is closing as the process flow gets close to the required minimum, there is a very critical operating mode when the multistage throttles completely lose their efficiency and the complete pressure reduction (>200 bar) is concentrated only on a small gap between piston and piston seat. In this single stage pressure reduction mode, the pressure inevitably falls below the vapor pressure and cavitation occurs with severe consequences for the bypass trim. Thus, the matter of point on ARV design is NOT to make pressure drop below vapor pressure at each pressure reduction throttle stage at any flow rate.
In 2015, Schroeder as the first ARV manufacturer was successful in solving the problem described above. By using a sophisticated hydraulic control system, the newly developed SHP series could avoid this wear critical bypass operating mode, even without any restrictions of the main flow range or the pump operating mode, as it is common for classic AR Valves. In the next step in 2017, this hydraulic control system was transferred to the SIP with a simpler and consequently more competitive technical concept.
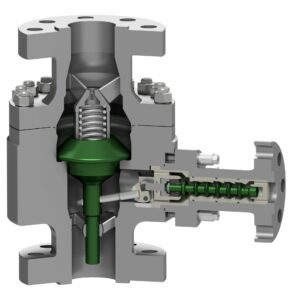
Since being operated in 2015, the plant had been suffering from AR Valves which design is suitable for regular operation at Q100, not for variable operating conditions – especially for partial-load operation which might bring extremely critical cavitation problems in the ARV’s internal parts of the bypass branch. And so, the plant had investigated which is the best solution among control valves, other automatic recirculation valves and the Schroeder Valves SIP series. Schroeder finally got the chance to demonstrate their SIP on this very challenging application because of the following reasons:
- The SIP bypass branch design is exactly the same as at the SHP valves that have shown very good performance at other CCPPs – Osung CCPP & Ansan CCPP in South Korea since their installation in 2018.
- The Schroeder Intermediate Pressure Valve (SIP) is especially designed for intermediate to high pressure applications from 100 bar up to 250 bar with frequent plant operation below minimum flow rate conditions.
- The SIP controls the bypass by means of a multi-stage piston and a sophisticated hydraulic control, which enables a defined multi-stage pressure reduction at all flow rates and avoids the most critical operating modes. This stands for almost cavitation-free or very light cavitation operation at all times.
After almost 10 months, where nearly half of the operation time was operated in modulating bypass position (partial-load operation), the SIP was disassembled to be thoroughly inspected on the internal parts and they almost looked brand new.
It is understood that a large number of those plant types suffer from the ARVs causing malfunctions that result in short lifetime of internal parts and, in return, require high maintenance time and cost.
Schroeder Valves in Germany is confident that SIP can be an ideal solution to respond to various operation load changes and is completely in line with their customers’ expectations. SIP can provide valuable benefits to customers, representing a care-free and durable operation at low maintenance and a favorable energy balance.
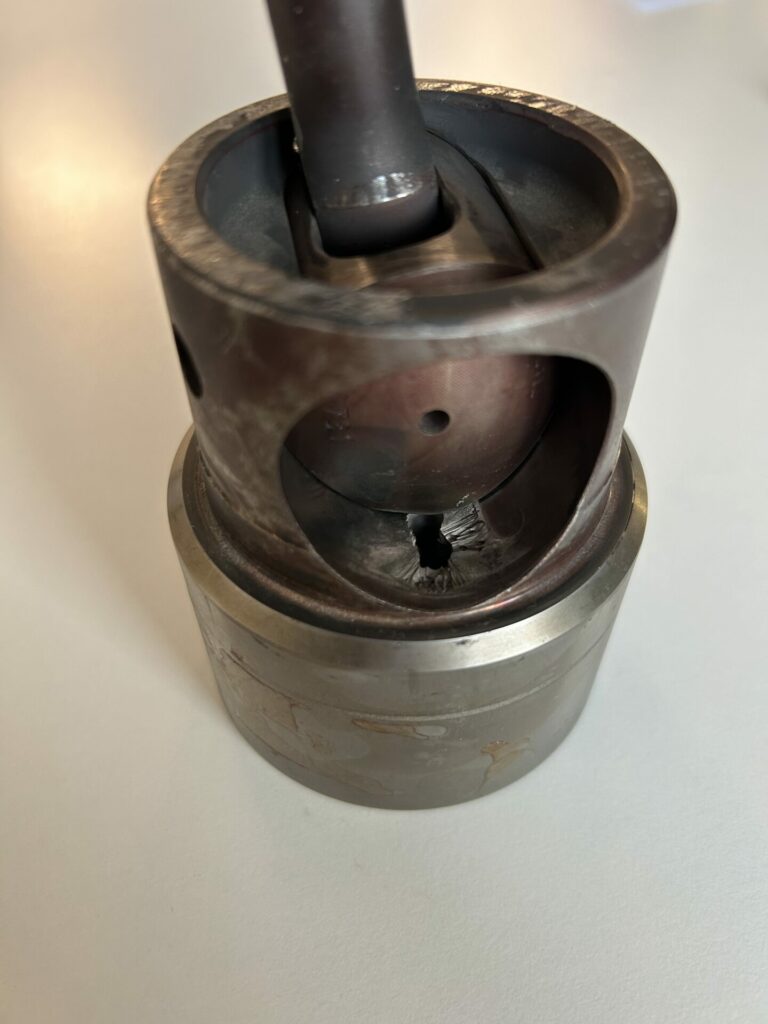
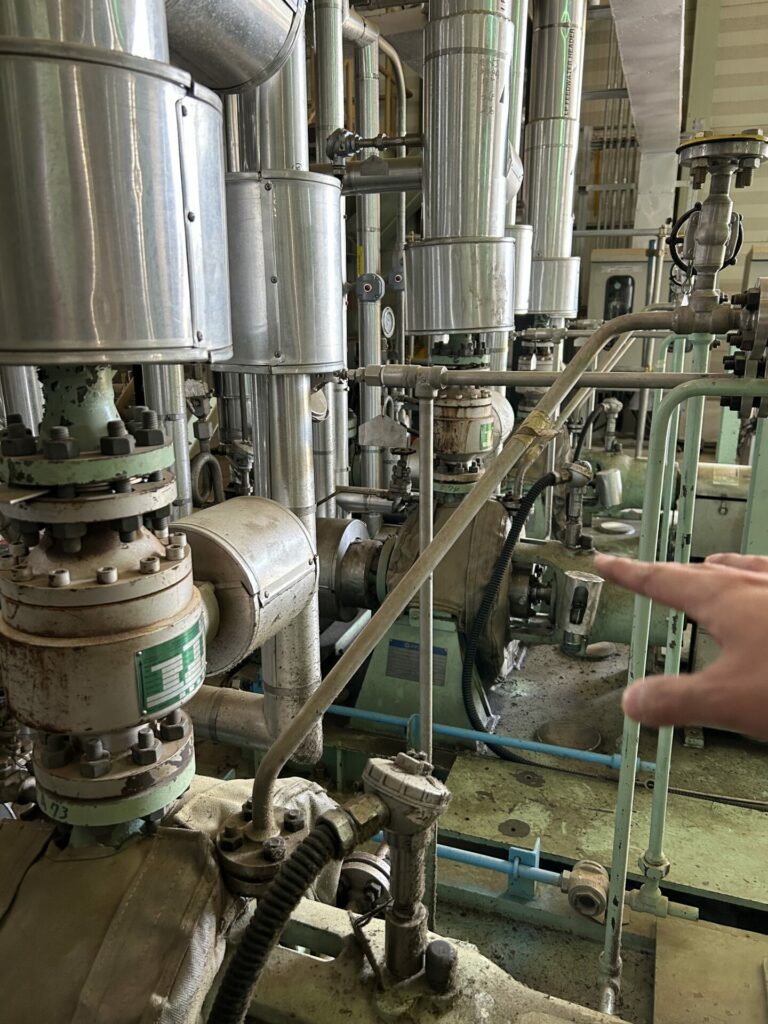
Source of Article