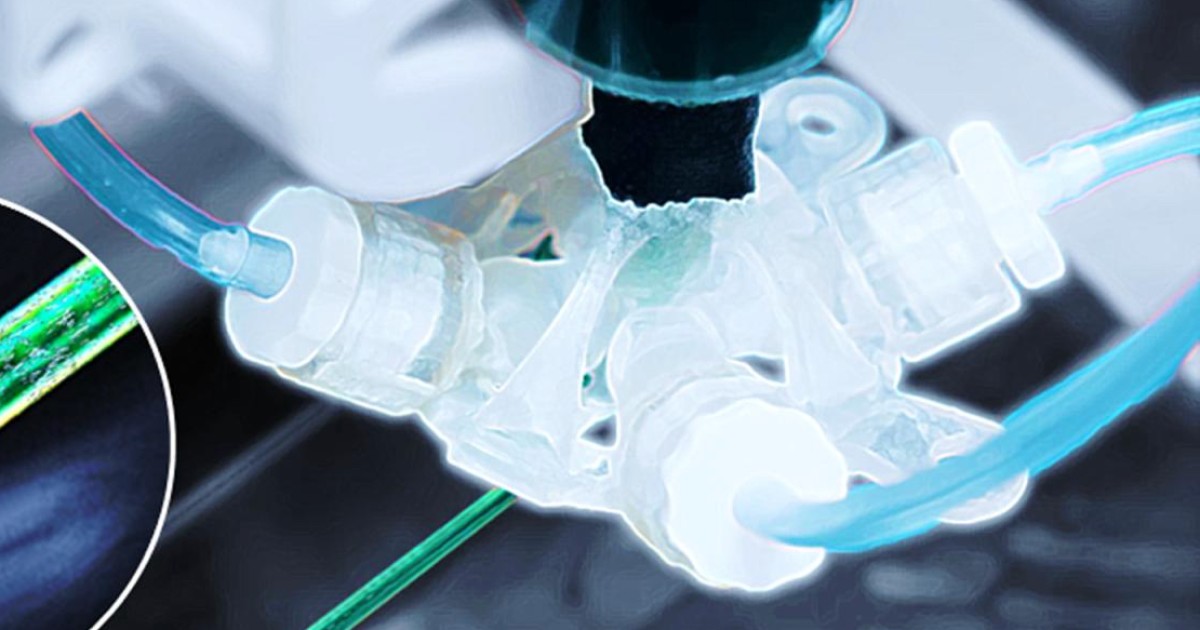
The embedding of fibers within 3D-printed objects can be used to add properties such as electrical conductivity or extra strength to those items. Now, a shape-changing print nozzle has been developed to vary the orientation of those fibers – as the printing is in process.
Ordinarily, short fibers of functional materials such as carbon are simply mixed into the print medium, then extruded along with it. As a result, they typically end up in a random jumble relative to one another. This is OK for some applications, but not for others.
Seeking an alternative that allowed for more control, engineers at the University of Maryland utilized a “PolyJet Printing” process to create a prototype print nozzle that has inflatable actuators along its sides. By selectively pumping air in and out of these, the shape of the nozzle changes, altering the orientation of fibers within a single print medium that it continuously extrudes.
In a test of the device, structures were printed out of a hydrogel containing carbon microfibers. In some areas, the relatively random orientation of the fibers caused the material to swell equally in all directions when it absorbed water. In other regions, the more aligned fiber orientation caused the material to swell primarily in one direction.
The technology could find use in a field known as “4D printing,” in which 3D-printed objects change form in response to external stimuli. It could also be utilized for more traditional 3D-printed items that have different elastic, thermal, magnetic or electrical properties in different areas.
“By providing researchers with an accessible way to 3D print fiber-filled composite materials with on-demand control of their fiber orientations, and thus, their ultimate performance, this work opens the door for new applications of 3D printing that harness these unique material properties and the distinctive capabilities they enable,” says Asst. Prof. Ryan Sochol.
A paper on the research, which was led by Connor Armstrong, was recently published in the journal Advanced Materials Technologies.
Source: University of Maryland via EurekAlert
Source of Article