Inline reaction monitoring where only little space is available or under harsh conditions is an urgent calling matter – especially for R&D applications. The selection of precise analyzer for laboratory vessels, small process reactors and technical center presents the user with a major challenge.
On the one hand the analyzer should be as space-saving as possible, on the other hand the device must withstand harsh and changing process conditions. Especially for R&D and process up-scaling tests specific parameters must be changed and inline monitored: high temperature levels, pressure drops, fluctuations in concentration level, process interruptions by impurities, secondary components etc.
In consideration of the customer requirements, SensoTech GmbH has designed the LiquiSonic® Lab 3-in-1-sensor. This model is designed for reactors and small plants in laboratory and technology centers. Directly flanged into the reactor lid, sonic velocity, attenuation and temperature are monitored with high precision. LiquiSonic® provides an opportunity for complex polymerization or crystallization reactions monitoring, e.g. in down-scale reactors. Even harsh conditions like high temperature or pressure are successfully mastered. Figure 1 shows the installation into a small reactor with an agitator or further equipment. The sensor is fixed into the reactor lid and fits through every fitting >12mm. Process kinetics can be monitored inline and even under extreme process conditions in such pressurized miniplants or pilot reactors. Space-saving design, separated sensor electronics and a user-friendly, multilingual controller with powerful data memory characterize the LiquiSonic® system.
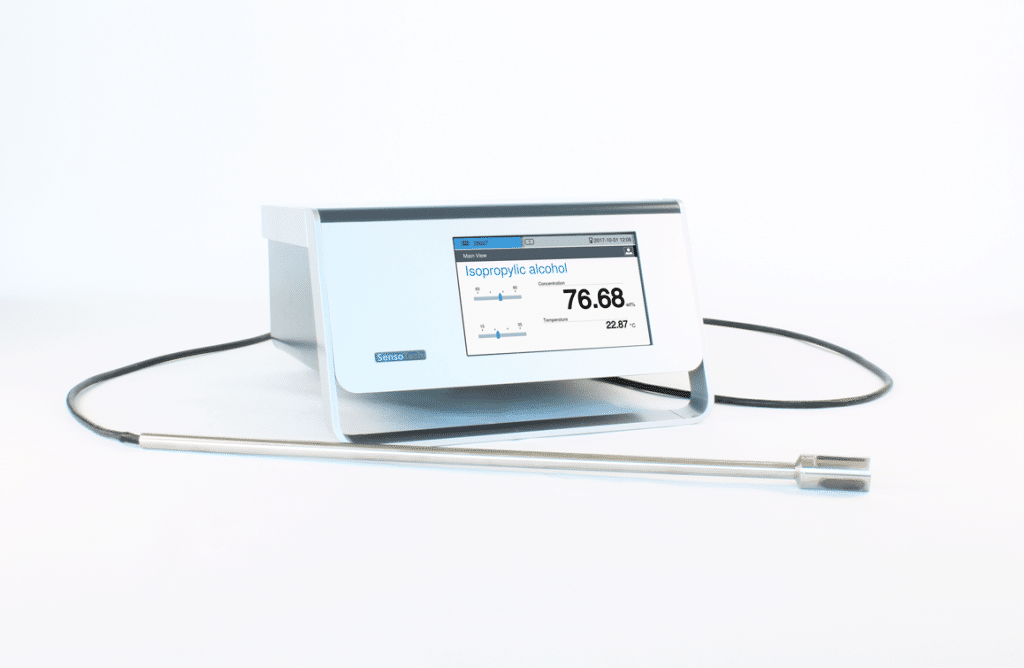
Typical measuring tasks are concentration monitoring, reaction monitoring, characterization of new-designed ingredients, detection of process trends like crystal nucleation and many more. The LiquiSonic® Lab sensor is a 3-in-1 all-rounder: sonic velocity, attenuation and temperature are measured in real-time. Especially, to monitor R&D processes or new designed active pharmaceutical ingredients this physical parameters are essential tools. Further the evaluation of nucleation and saturation curves of numerous mother liquors and the monitoring of crystal content [%] are typical applications. Even tricky polymerization processes can be tested in small-scale. The changing sonic velocity and attenuation indicate the polymerization degree. The results from such laboratory reactor or pilot plant studies are of use for process optimization in large-scale processes, where typically also ultrasonic analyzers are installed.
The LiquiSonic® Lab 3-in-1-sensor (see Figure 2) impresses customers worldwide with its design for small reactors and innovative technology. Installations up to 160°C and 16bar are solved easily. Further, the system is well-equipped for measurements in highly viscous suspensions. Special sensor materials like Hastelloy HC2000, tantalum or titanium protect against corrosion and promote long process life. All physical parameters and powerful diagnostic capabilities are logged 24/7 into the internal long-time memory. This way, applications in R&D laboratories and technical centers easy and bring innovative solutions for up-scaling and process optimization.
Result
Measuring systems of SensoTech GmbH are made for challenging requirements so that also complex installations and measuring tasks can be met. The high-precision LiquiSonic® Lab 3-in-1-sensor is measuring sonic velocity, temperature and attenuation in various customized applications. Even complex R&D applications and reaction monitoring in laboratories and technical centers with high temperature and pressure levels are managed easily.
Click here for more informationClick here for related articles and news
Sign up for Fluid Storage E-Updates
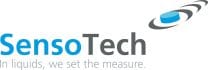
Manufactured in Germany, the main principle of our innovative systems is to measure ultrasonic velocity and density in continuous processes. We have perfected this method into an extremely precise and remarkably user-friendly sensor technology. As well as the measurement of concentration and density, typical applications include phase interface …
Source of Article