While multi-material 3D printers do already exist, the filament that they extrude is typically all one material at any one point in the printing process. A new system produces actual multi-material filaments, however, and they boast a potentially very useful helical design.
The experimental setup was developed by a team at Harvard University led by Prof. Jennifer Lewis, Prof. David Clarke and postdoctoral student Natalie Larson.
Its printhead incorporates four separate cartridges, each one of which can contain a different “ink” (photo-curable viscous printing material). All four cartridges feed into one nozzle, which extrudes a single filament made up of continuous strands of all the inks.
Because the nozzle rotates throughout the extrusion process, the strands spiral around one another in a twisting helical pattern. This same pattern is often seen in nature, where it allows muscle fibers to contract, and plant stems to change shape. Of course, it’s also the form taken by DNA strands.

Natalie Larson, Lewis Lab at Harvard University
In one experiment, the scientists created artificial muscle filaments in which a couple of conductive elastomer strands – serving as two electrodes – spiraled around one another within a soft elastomer matrix. When a voltage was applied to the filament, it responded by contracting. The extent to which it contracted depended on how tightly the helical electrodes were coiled when printed.
The researchers also created lattice-like structures consisting of cross-woven filaments which served as springs. Again, by varying how tightly the strands within those filaments were coiled, it was possible to adjust the springiness of the filaments, as thus of the whole lattice. Such structures could conceivably be used as hinges or joints in soft robotic devices.
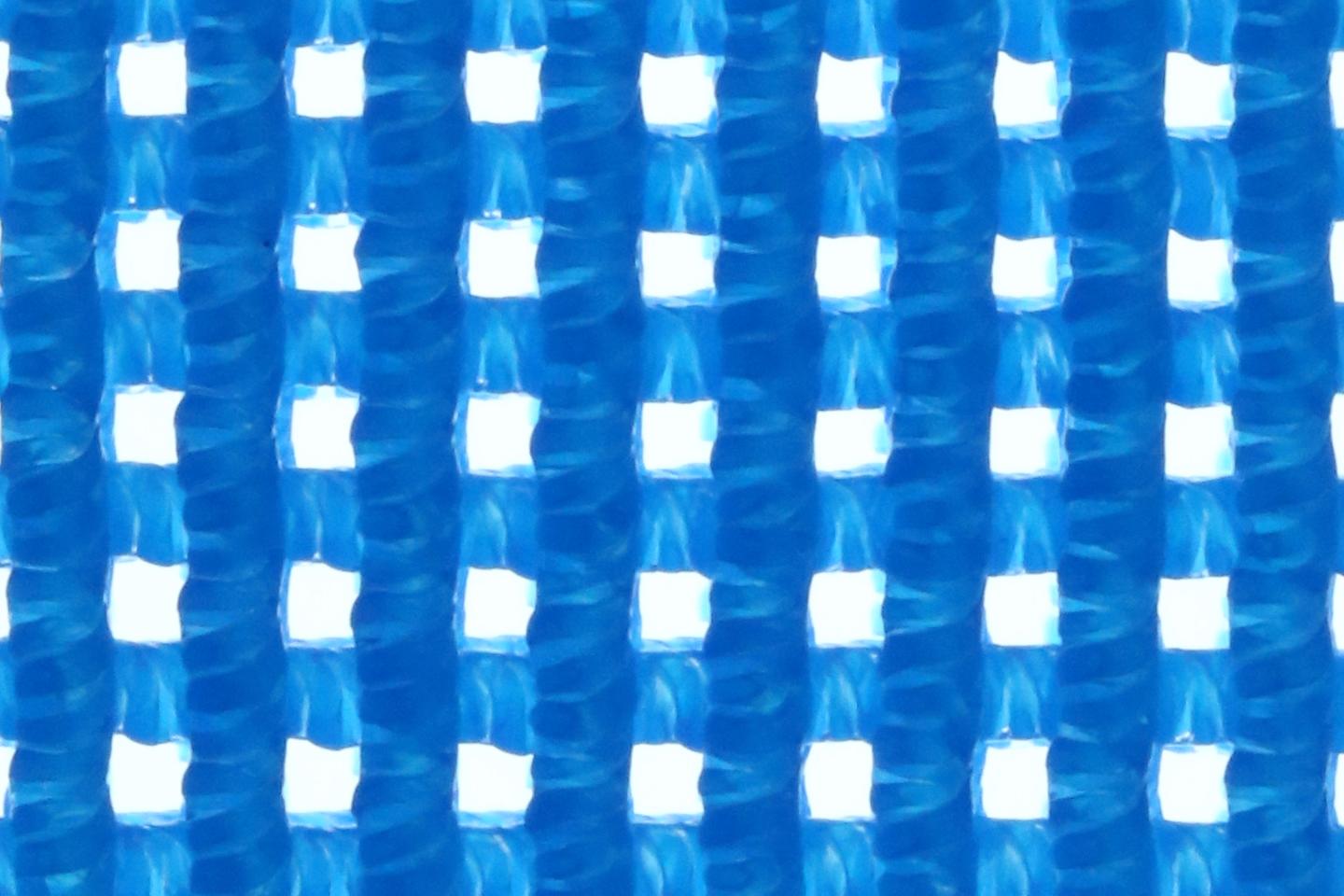
Natalie Larson, Lewis Lab at Harvard University
The team is now refining the technology, with an eye towards other possible applications.
“By designing and building nozzles with more extreme internal features, the resolution, complexity, and performance of these hierarchical bioinspired structures could be further enhanced,” said Larson.
A paper on the study was recently published in the journal Nature.
Source: Harvard John A. Paulson School of Engineering and Applied Sciences
Source of Article