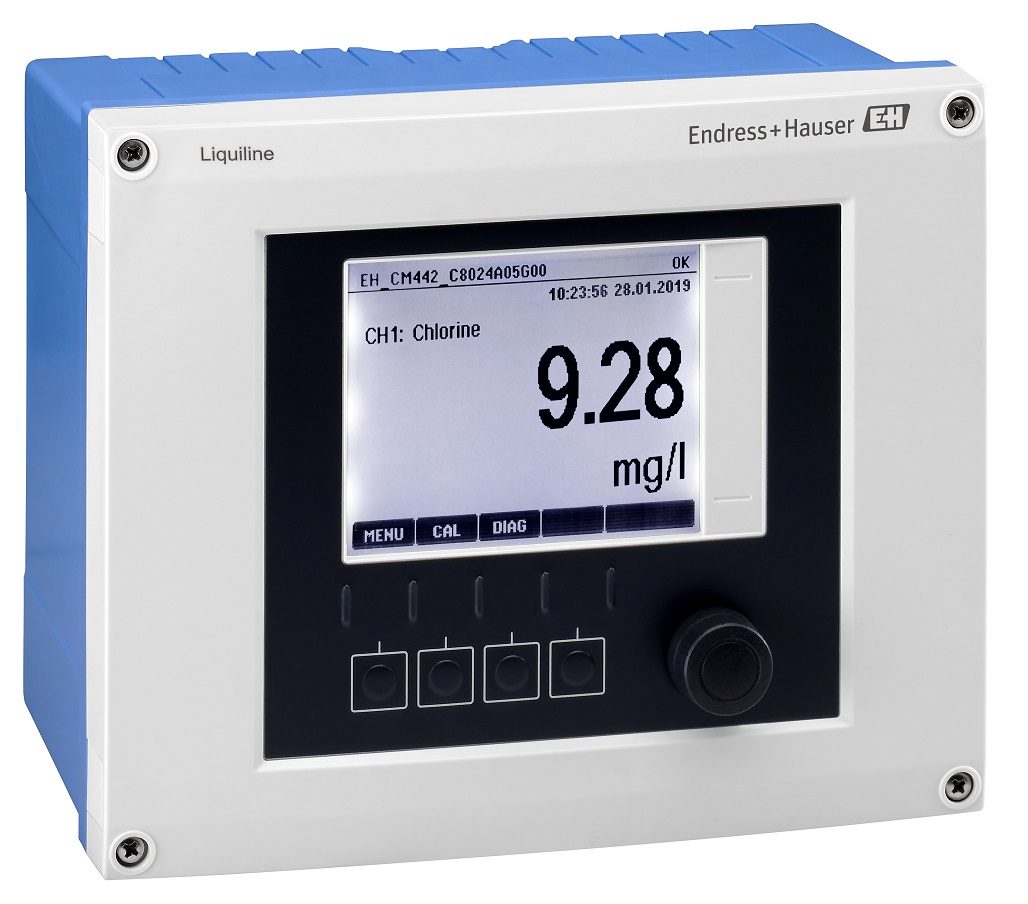
In many cases disinfection of the raw water occurs downstream from the reverse osmosis process. The disinfection process utilizes 0.3 mg/l of free chlorine, which corresponds to the allowable amount as outlined in the German drinking water regulations. The raw water is then freed of all residual chlorine via filtration since it must be completely free of chlorine before adding the beverage syrup.
However, this filtration is circumvented via a bypass once a week in order to clean the piping with chlorine at low temperatures using a so-called cold cleaning in place (cold CIP) process.
In order to monitor the removal of the chlorine and the cold CIP process, amperometric sensors are installed at two points to measure the amount of free chlorine:
- after filtration to determine if the water is chlorine-free
- in the piping system where the chlorine content must be maintained at 0.3 mg/l.
The special challenge here is the absence of chlorine over a longer period of time after filtration. With many amperometric sensors, this absence leads to a delayed response behavior, with the sensor essentially falling asleep. This can lead to product loss since the beverage syrup is added while undetected chlorine is present in the raw water after filtration. The Memosens CCS51E sensor from Endress+Hauser for measuring free chlorine exhibits no delayed response even after a longer period of inactivity, thus ensuring that any chlorine peaks do not go undetected. The sensor furthermore “notices” chlorinated water once a week when the filtration is bypassed. This tests the functionality of the sensor and ensures electrochemical activation. Compared to wet chemical analyzers that use the DPD method, which can provide a measurement value only every three minutes, inline measurements with amperometric sensors offer continuous measurements in which no peaks are overlooked.
Continuous measurements are furthermore beneficial for controlling the chlorine dosage. The fast measurement value means a more precise dosage: as little as possible, but enough for a reliable disinfection process. Achieving this degree of precision requires creating an adequate flow to the sensor membrane of 15 cm/s. If the sensor is calibrated once a year, the DPD calibration should be carried out by drawing the sample near the sensor, keeping the cuvette clean, observing the expiration date of the DPD reagents and avoiding air bubbles in the sample.
The amperometric sensors require no reagents, making them low maintenance. The new generation of Memosens sensors also stores more data regarding calibration and operating hours – such as the electrolyte counter – and the load, making it possible to develop a more efficient maintenance strategy tailored to the application.
Source of Article